模具制造技術現狀與發展趨勢
2018-12-20 來源:華南理工大學 聚合物成型加工工程 等 作者:劉 斌 崔志杰 譚景煥 吳松琪 柳亞強
摘要:基于模具制造技術的研究,首先介紹了應用于模具制造行業的加工制造技術,包括特種加工、數控加工、柔性制造和快速制模等技術;接著對相應的CAM軟件、模具生產管理類軟件等模具制造相關軟件及數控系統的發展趨勢進行詳細介紹;然后對模具制造行業所使用的夾具和機床主要品牌及其制造企業進行總結;最后提出模具CAM、模具加工設備和數控系統都將向智能化、網絡化、高精度和高效率方向發展的趨勢。
關鍵詞:模具制造;數控系統;CAM軟件;加工機床;發展趨勢
0 、引 言
模具制造是指在特定的制造裝備和工藝下,直接對原材料進行加工,使之成為具有一定形狀和尺寸要求的零件,然后裝配成模具的過程,即模具零件的加工和裝配過程。模具制造行業屬于離散型制造業,其過程復雜,具有單件生產、制造質量要求高、形狀復雜、材料硬度高等特點。模具零件的制造加工方法有常見的金屬切削加工、電化學加工和電火花加工,同時還有精密鑄造、激光加工、其他高能波束加工以及集2種加工方法為一體的復合加工等。隨著數控技術和計算機技術的發展,其在模具零件的加工中應用越來越廣泛。
1 、模具制造技術
1.1 特種加工方法
模具制造常用的特種加工方法有:電火花加工、激光加工、超聲波加工、電子束加工、模具電鑄成形等。
1.1.1 電火花加工
電火花加工是利用電蝕作用去除導電材料的加工方法,又稱放電加工或電蝕加工。加工時工件和工具電極同時浸泡在絕緣工作液中,并在兩者之間施加強脈沖電壓,以擊穿絕緣工作液,由于能量高度集中,放電區的高溫使工件表面金屬局部熔化脫落,達到去除材料的效果。電火花加工主要分為電火花成形加工和電火花線切割加工。
(1)電火花成形加工。電火花成形加工在模具行業應用廣泛,尤其適用于手機、汽車等注射模零件加工。隨著零件加工精度、粗糙度要求的不斷提高,電火花成形機的需求也增加。電火花成形機的優勢:放電加工控制系統可實現 4 軸聯動或 5 軸聯動加工,實現機床加工的高精度(重復定位精度≤2μm)、高效率(切割速率≥500 mm/min)、低表面粗糙度(Ra≤0.1 μm)、低電極損耗率(≤0.1%)、任意軸向的抬刀和伺服放電加工、復雜的4軸聯動加工。
(2)電火花線切割加工。線切割加工是電火花加工的一種,電極是細長金屬絲,金屬絲在移動同時進行脈沖放電使其附近的金屬局部熔化脫落,通過控制金屬絲的移動軌跡即可切割相應的圖案。高速走絲線切割使用鉬絲作為工具電極,其直徑為0.02~0.3 mm,往復移動速度達 8~10 m/s。低速走絲線切割使用銅絲作為工具電極,其移動速度較慢,一般<0.2 m/s,且單向運動。相比于電火花成形加工,線切割加工精度高,約為10 μm。慢走絲精度可達0.5 μm,表面粗糙度約Ra 0.2 μm。快走絲精度可達 20 μm,表面粗糙度約 Ra3.2 μm。電火花線切割適用于加工沖孔模和落料模等零件上的各種???、型孔、復雜型面、樣板和窄縫等。
1.1.2 激光加工
激光加工是材料加工部位在高能激光束的照射作用下加熱至高溫熔融狀態,并使用沖擊波將熔融物質噴射出去的加工方法,或是使材料在較低能量密度的激光束作用下熔化,然后進行焊接的加工方法。在模具行業,尤其是在模具修復和模具制造方面,激光加工應用廣泛,常見的有激光切割、激光打孔、激光淬火和激光焊接等。同時激光加工技術還能應用在表面強化處理方面,主要有2種方式:一是利用激光熔焊對模具表面局部損傷部位進行修復;二是利用激光對模具表面進行淬火硬化。
1.1.3 超聲波加工
超 聲 波 是 指 頻 率 超 過 人 耳 頻 率 上 限(>16k Hz)的振動波。超聲波加工是利用超聲波作為動力,帶動工具作超聲振動,通過工具與工件之間的磨料沖擊工件表面進行加工的成形方法。采用超聲波-電化學拋光復合加工工藝拋光模具型腔表面,不僅可以提高模具型腔表面質量和降低表面粗糙度,還能提高生產效率,減少工具的損耗。
1.1.4 電子束加工
電子束加工是指通過真空環境中的高能電子束將工件待加工部位加熱至熔融或蒸發的狀態,達到去除材料的加工方法。同時,利用高能電子束提供能量使工件表面發生化學反應,也是電子束加工的一種應用。將帶有脈沖電壓的電子束照射在模具零件表面,可以對模具零件表面進行拋光處理,是一種新型的模具零件表面處理工藝。
1.1.5 模具電鑄成形
電鑄成形是利用電化學過程中的陰極沉積現象進行成形的加工方法,主要用于注射模零件的加工。注射模的電鑄成形是將動模作為陰極,將需要電鑄的金屬作為陽極同時置于鍍槽中,然后通入直流電,此時陽極的金屬釋放金屬離子,并向動模沉積,一段時間后,動模上會沉積有適當厚度的金屬層,形成電鑄層。電鑄工藝適用于金屬型腔的復制加工,且加工精度高。
1.2 數控加工技術
1.2.1 模具零件數控加工
模具作為成型塑件的工具,其零件制造精度要求高于成型塑件的精度。組成模具的大部分零件一般具有復雜的型面,傳統的加工方法不僅加工效率低,且加工精度低。數控加工是模具零件加工的主要方法,如數控車削加工、數控銑削加工、數控線切割加工、數控電火花加工等。
(1)數控車削加工。數控車削可用于頂桿、推桿、導柱、導套等軸類零件的加工;還可用于回轉體模具零件的加工,如外圓體、內圓盆類零件的注射模零件,軸類、盤類零件的鍛模以及沖模的凸模等。
(2)數控銑削加工。數控銑削可用于外形輪廓較為復雜或者帶有三維曲面型面的模具零件的加工,如注射模的型芯、型腔板的加工等。
(3)數控線切割加工。數控線切割可加工各種直壁模具零件或者一些形狀復雜、材料特殊以及帶有異型通槽的模具零件。
(4)數控電火花加工。數控電火花加工可用于微細復雜形狀、特殊材料、鑲拼型腔板及鑲件、帶異型槽的模具零件的加工。
(5)數控加工中心加工。數控加工中心根據加工軸數可分為3軸、4軸和5軸等,其中,5軸數控加工中心可以加工高精度、曲面復雜的模具零件。目前,在模具零件加工中,5
軸數控加工中心應用較廣泛。
1.2.2 國內外數控系統
國內外有名的數控系統有:發那科(FANUC)、馬扎克(MAZAK)、三菱(MITSUBISHI)、西門子(SIMENS)、發格(FAGOR)、西曼斯(CMS)、華中數控(HSK)、廣 州 數 控(GSK)、寶 元(LNC)、新 代(SYNTEC)等,如表1所示。
表1 國內外數控系統
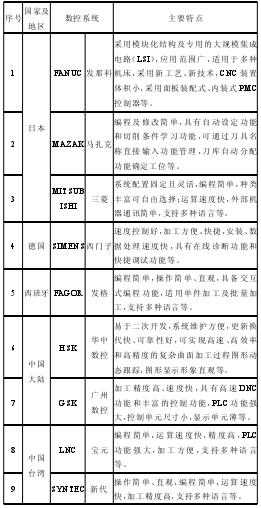
一些國外知名廠家采取技術封鎖和低價銷售的策略,利用靈活多樣的促銷手段和先進的技術以及優質的產品迅速搶占中國市場。目前,國內普及型、中、高檔數控系統的市場已經被國外品牌壟斷。但國外的數控系統有如下缺點:
(1)維修費用高,維修時效性低,系統更新慢。
(2)技術封鎖,數控系統二次開發難度大。
(3)與國內數控機床相比價格昂貴,性價比低。隨著國內數控系統公司不斷創新,國內數控技術的發展取得了跨越式進展。目前,我國的數控系統與國外相比雖有差距,但差距正不斷縮小,如廣州數控、華中數控等,正在積極發展自己的核心技術。
1.3 柔性制造技術
1.3.1 柔性制造單元
柔 性 制 造 單 元(flexible manufacturing cells,FMC)是數控加工中心的擴展,數臺數控機床或加工中心和工件運輸裝置在計算機系統的控制下,根據需要自動更換夾具和刀具,進行工件的加工。FMC 主要有以下 3 種類型。
(1)托板存儲庫式 FMC,其特點是有托板儲存系統,可通過 PLC 控制托板的選擇和定位,適用于非回轉體零件的加工。
(2)機器人搬運式FMC,由加工中心、數控機床機器人和工件傳輸系統等組成,有些單元還包括清洗設備。
(3)可換主軸箱式 FMC,一般由可更換主軸箱的數控機床、主軸庫、主軸交換裝置和托板交換裝置組成。裝有工件的托板交換裝置將工件運送至圓形工作臺上夾緊,裝有主軸箱的動力頭驅動刀具加工工件??蓳Q主軸箱式 FMC 的加工方式為多軸加工,適用于中、大批量的工件加工生產。
1.3.2 柔性制造系統
柔性制造系統(flexible manufacturing system,FMS)主要由數臺加工中心、工業機器人和自動制導小車(AGV)等組成,在計算機的控制下,實現對同的加工對象的自動化機械制造。柔性制造系統的優勢有:
(1)設備利用率高。相比于機床分散式單機作業,成組的機床編入柔性制造系統后,生產效率可以提高數倍。
(2)產品數量減少 80%左右。柔性制造系統一般包括多個工序,每個產品在生產組裝時無需等待就能進入下一工序,從而使等待加工的產品數量大幅度減少。
(3)生產能力穩定。柔性制造系統包含一臺或多臺機床,當某一臺機床發生故障時,能實現降級運轉,同時,物料傳輸系統能自動繞過故障機床,避免生產線停產。
(4)產品質量高。加工時工件只需一次裝夾,就能完成各工序的加工,加工精度高、穩定性好。
(5)運行靈活。柔性制造系統的檢驗、裝夾和維護工作都可以在第 1 班完成,可實現第 2 班、第 3班自動化生產。對于功能更加完善的柔性制造系統,刀具的磨損更換、物流的堵塞疏通等問題都能在監控系統作用下解決。
(6)產品應變能力大。夾具、刀具和物料傳送裝置的柔性大,系統的可擴展性強,能通過增加或減少設備,實現不同產品的生產。
(7)經濟效益顯著FMS能根據裝配作業的需要及時調整所需零件的加工,達到及時生產的效果,避免了毛坯的囤積,降低了流動資金的占用量,提高生產效率。同時,在相同的生產能力下,較高的設備利用率能減少設備需求和廠房面積,且FMS能在人員數量少的情況下實現自動化連續生產,降低勞動力的需求,FMS生產的產品質量大幅度提高。
1.4 快速制模技術
與傳統模具零件加工技術相比,快速制模技術能以較低的生產成本以及較高的效率,制造出較高精度和耐用性的模具,是一種經濟效益良好的先進制造技術。
(1)3D打印技術。3D打印屬于增材制造(addi-tive manufacturing,AM)技術,是激光技術、材料科學技術、計算機技術、數控技術高度發展的產物。3D 打印技術與傳統去除材料的加工方法不同,其采用“分層切片,層層疊加”的原理,只需要把產品 3D模型通過指定的方式傳輸到 3D 打印設備,就可以打印出具有一定精度的產品。相比于傳統制模技術,3D打印技術的制造效率高,成本低,適用于新產品的開發研究。
3D 打印技術包括激光立體光刻成型(SLA)、分層物體制造(LOM)、選擇性激光熔化(SLM)、熔融沉積成型(FDM)等多種成型工藝。3D打印制造模具實例及鑲件如圖1所示。
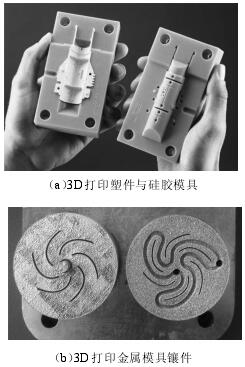
圖1 3D打印制造模具實例及鑲件
(2)表面成形制模技術。表面成形制模技術可用于型腔表面或精細花紋的加工,涉及的工藝技術有電鑄、噴涂、化學腐蝕等。
(3)澆鑄成形制模技術。澆鑄成形制模技術主要有鉍錫合金制模技術、鋅基合金制模技術、樹脂復合成形技術及硅膠制模技術等。
(4)冷擠壓及超塑性成形制模技術。冷擠壓是模具型腔板的一種加工方法,不需要切削加工,只需將堅硬的原?;騽幽=涍^冷擠壓壓入較軟且塑性好的材料內,形成所需的型腔。經冷擠壓加工形成的型腔表面光滑,可縮短擠壓后的加工過程。采用冷擠壓、冷滾壓加工方法加工復雜型腔或型面的新工藝,由于效率高、質量好,廣泛用于制造塑料、壓鑄、熱鍛、精壓、冷鐓、冷沖、螺紋滾壓等各種模具零件。
(5)無模多點成形技術。通過對一系列排列規則、高度可調的基體的實時控制,自由地構造成型實現板材曲面加工,是集計算機技術和多點成形技術于一體的復合制造技術
(6)隨形冷卻技術。注射模中,冷卻水道可以根據塑件形狀設計成相應的形狀,水道直徑可以根據需要改變,水道截面形狀的選擇呈多樣化。模具冷卻時間是決定塑件生產周期長短的重要因素,通過CAE分析優化模具冷卻水道的形狀和布置方式,可以提高冷卻效率,并降低因冷卻不均導致的廢品率。目前,隨形冷卻水道主要通過選擇性激光熔化(
SLM)技術制造,具有隨形冷卻水道的注射模如圖2 所示。
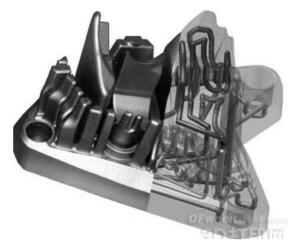
圖2 隨形冷卻水道的注射模
2 、模具制造相關軟件
2.1 CAM 軟件
目前,常用的 CAM 軟件有:UG NX、Master-CAMPower MILL、Cimtron、Solid CAM、CAXA、SINOVATION、中望 CAM 等等。
2.1.1 國外 CAM 軟件
(1)UG NX。UG NX 是德國西門子公司設計的具有強大造型功能和數控編程功能的軟件。該軟件曲面造型功能強大,具有完善的系統庫,適用于模具設計和數控編程。
(2)Master CAM。Master CAM 是由美國 CNCSoftware Inc.公司基于 PC 平臺開發的集三維實體造型、體素拼合、數控編程、刀具路徑模擬等多種先進功能于一體的軟件。
(3)Power MIL。 Power MILL 是 英 國 Delcam公司開發的高度智能化的 CAM 系統,具有基于知識和工藝特征的多種加工方式,同時具備加工過程防過切、高速加工等功能,可進行5軸加工編程。
(4)Cimatron。Cimatron 是以色列 Cimatron 開發的軟件,具有模具設計、NC 編程與加工、3 軸加工、殘料加工、插銑加工、高速銑削、智能NC等功能。
(5)Solid CAM。Solid CAM是以色列Solid CAM公司開發的軟件,具有2.5軸銑削、3軸銑削、多面體4/5 軸定位銑削、高速銑削(HSM)5 軸聯動銑削、車削和高達5軸的車銑復合加工、線切割等編程模塊。
2.1.2 國產CAM 軟件
(1)CAXA。CAXA 是北京數碼大方科技有限公司自主研發的軟件,其數控加工模塊具有加工多樣化(2~5軸)、高速加工、參數化軌跡編輯及軌跡批處理、獨特的加工仿真與代碼驗證、加工工藝控制等特點。
(2)SINOVATION。SINOVATION 是山東山大華天軟件有限公司開發的軟件,具有特征造型、CAM 加工、沖模設計、注射模設計、沖壓工藝設計等功能模塊,其中,CAM 加工模塊支持2軸、3軸、5軸數控銑削加工,具有強大的路徑編輯功能和參數化后處理工具。
(3)中望 CAM。中望 CAM 是廣州中望龍騰軟件股份有限公司研發的軟件,包含粗加工、精加工、螺紋加工、凹槽加工、端面加工、鉆削加工、切斷加工等加工方式,具有工藝管理方便、加工刀具路徑合理、操作簡單、支持5軸加工等特點。
2.2 模具生產管理軟件
模具企業中常用的生產管理軟件是企業資源規劃(enterprise resource planning,ERP)[18],于 1990年由美國 Gartner Group 公司研發成功。隨著模具企業的迅速發展及生產經營的擴大,信息化管理技術需求也越來越大。為了使設計、生產、管理等能夠適應企業的發展,必須在人力資源、物流、信息等方面加強計算機技術的集成,在產品設計、生產管理、財務控制、經營決策等各方面實行更加科學地管理,取得更高的經濟效益。目前,模具企業的內部資源比較分散,人力資源、生產制造、生產管理等方面通常采用不的軟件,降低企業內部資源管理的效率。開發集 CAD、PDM、ERP 等各類信息技術于一體的系統,能夠實現企業的內部集成與協同,有利于研究開發模具企業的 ERP 系統。以下介紹模具行業常用的 ERP 軟件。
(1)SAP。SAP是一款由德國SAP公司開發,能對企業的后勤、人力資源、財務、業務工作流程等進行統一的管理的ERP系統,具有功能性、靈活性、開放性、用戶界面友好、模塊化、可靠、低成本、高效益、多語言支持等特點,廣泛應用于模具行業。
(2)EMAN。EMAN 是武漢益模軟件科技股份有限公司開發的,針對模具企業的生產特點和生產過程量身定做的信息化管理系統。該系統以模具生產過程的管理為核心,以保證質量、降低成本和縮短模具生產周期為目標,可通過簡單的操作幫助模具企業的相關人員完成模具生產過程的有效管理。
(3)方天Mold ERP。方天是臺灣方天軟件科技股份有限公司研發的ERP軟件,該軟件具有模具設計系統、模具 MES 系統、模具項目管理系統、模具自動排程系統、模具車間執行系統、模具外發加工管理系統、模具質量檢測系統、模具財務管理系統等模塊,以模具制造過程為管理核心,降低模具制造成本、縮短模具生產周期、保證產品質量為目標,通過簡單的操作完成對模具生產過程的有效管理。
(4)Team-link MES。Team-link MES是由深圳市世紀天揚科技有限公司開發的模具精益生產管理系統,具有模具檔案集中管理、模具領用歸還統一控制、模具使用壽命自動累計、模具位置標識歸
位、模具保養自動提醒等特點,能夠對模具狀態進行實時監控,減少誤用損壞模具、損壞模具停產的現象,節省模具準備時間,降低模具生產的時間成本。
(5)TOP-THINK。TOP-THINK 軟件由深圳市杰納斯科技有限公司開發的ERP軟件,主要服務于注射、吹塑、沖壓、組裝、線材、醫藥等行業。
3 、模具夾具
模具制造過程中,主要夾具有:標準件加工用夾具、非標準件加工用夾具和電極加工用夾具等,其中,標準件加工用夾具與一般機械零件加工用夾具相同。模具企業常用的夾具品牌有以下5種。
(1)3R 夾具。3R 夾具是瑞典 System3R 公司開發的夾具,具有簡單易用、方便快捷、可在機外檢測、節省時間、工作效率高、產品質量好、節約成本、電極可下機檢測修改且二次上機不影響精度、重復定位精度高等特點。
(2)米思米夾具。米思米夾具是日本米思米集團生產的夾具,具有安裝拆卸方便、安裝精度高、重復定位精度高、工作效率高等特點,廣泛應用于模具制造行業。
(3)Hainbuch夾具。Hainbuch夾具是德國Hain-buch 生產的夾具,具有安裝拆卸方便、精度高、更換便捷快速、環保、強度高、外觀優美等特點,廣泛應用于車床夾具。
(4)Roehm 夾具。Roehm 夾具是德國 RoehmGmb H 公司制造的產品,主要包括:Roehm 卡盤、Roehm 閥、Roehm 鉗、Roehm 鎖緊套等。Roehm 夾具具有安裝拆卸方便、定位精度高、強度高等特點。
(5)EROWA 夾 具 。 EROWA 夾 具 是 瑞 士EROWA 公司的產品,具有簡單易用、裝卸方便、重復定位精度高、可機外檢測、設備利用率高等特點。
4 、品牌機床
模具制造中使用的機床主要有數控銑床、數控車床、加工中心、電火花、線切割、磨床、鋸床、鉆床、激光加工設備等。據行業初步調查,目前,在模具行業用得比較多的機床及品牌如表2
所示。
表2 模具行業常用的機床及品牌
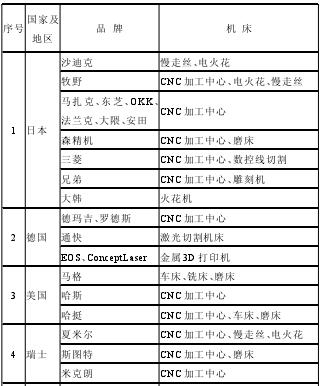
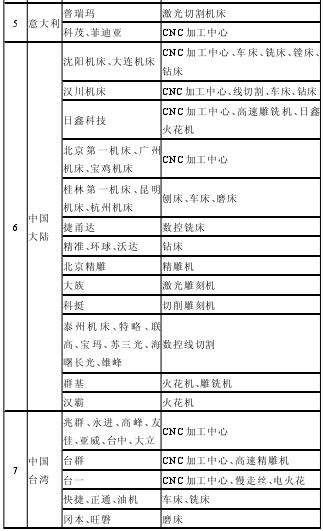
5 、模具制造發展趨勢
5.1 模具 CAM 發展趨勢
隨著計算機技術的發展,模具 CAM 的應用更加廣泛,其主要的發展趨勢包括以下3個方面。
(1)模具軟件功能集成化,模具生產中的設計、制造、裝配、檢驗、測試等環節實現信息的共享與綜合,產品的數據模型可以通過指定的協議傳輸到各個環節,模具軟件功能更加齊全。
(2)模具設計、分析及制作的三維化。使用三維軟件進行模具設計,且三維模型能夠在模具結構CAE 分析、數控編程、成型過程 CAE 分析等環節中共享,避免重復建模。三維設計過程直觀準確,有利于在生產前發現模具設計中不合理結構。常見的三維設計軟件有 Pro/E、UG 和 CATIA 等,這些軟件都具有參數化設計、基于特征全相關等特點,能
夠推動模具并行工程發展。
(3)模具軟件應用的網絡化趨勢。現在是信息化的時代,信息的共享能夠推動模具企業資源的合理配置,包括模具企業內部和外部的資源共享。將模具軟件接入網絡,不僅能夠提高模具企業內部信息傳輸的效率,還有利于促進企業間的合作與交流。在模具行業中推廣虛擬設計、敏捷制造等技術將是未來的重要發展方向。
5.2 模具加工設備發展趨勢
隨著模具制造技術的發展,模具加工設備也呈一定的發展趨勢,主要分為以下7大類。
(1)電火花加工機床朝著智能化、自動化、高效化、精密化的方向發展,如高精度的電火花成形機床、高效率的雙頭電火花機床等。電火花成形機床常用于復雜曲面的拋光加工,適用于模具型腔板的復雜曲面的精密加工,提高了模具加工效率。雙頭電火花機床加工大型模具時的效率是單頭火花機的2倍以上,廣泛應用于空調、冰箱、電視機、汽車等精密模具零件的加工。
(2)激光加工設備沿著更高精度、更高效率的激光拋光機和5軸聯動激光加工機床方向發展。激光拋光是使工件表面的薄層材料在一定波長和能量密度的激光照射下熔化或蒸發,以達到拋光效果的加工方法,彌補了傳統拋光方法很難或不能拋光復雜曲面的缺陷,適用于表面形狀復雜的模具零件的加工。5軸聯動激光加工機床是多軸激光微加工系統,能夠以超高精度加工各種模具零件,進行高精度激光切割、激光鉆孔、激光雕刻、激光焊接、激光燒蝕、激光皮紋加工等多種工作。
(3)高速銑削機床主要用于中、大型模具零件的加工,適用于具有復雜曲面的汽車覆蓋件模具零件、壓鑄模具零件、大型注射模零件的加工。目前高速銑削機床主軸轉速可達
100 000 r/min,加工精度可達0.01 μm,今后高速銑削機床將沿加工精度更高的方向發展。
(4)隨著3D打印技術的發展,金屬3D打印機逐漸應用于注射模隨形冷卻水道鑲件的加工、模具零件的加工制造及修復等。如DMT MX-250金屬3D打印機可用于隨形冷卻水道的復合制造,EOSINTM400 激光燒結 3D 打印機可用于批量生產模具零件、金屬零部件以及快速成型件等。
(5)柔性制造單元及系統朝多功能方向發展,如由單純加工型的柔性制造系統進一步開發以焊接、裝配、檢驗及板材加工或者鑄、鍛等制造工序兼具的多種功能柔性制造系統。
(6)高速、高精度加工技術及裝備加工速度更快、精度更高。部分超精密加工機床精度可達 0.01μm;數控機床的平均故障間隔時間>6 000 h,伺服系統的平均故障間隔時間
>3 000 h。為了適應加工設備的發展,其配套的零部件如電主軸、直線電機等發展速度也在加快,推動了高速、高精度加工的普及應用。
(7)隨著5軸聯動機床復合主軸頭結構的簡化,其制造難度和成本降低,5 軸聯動機床數控系統價格下降,且具備較高的加工效率和加工精度,復合主軸頭5軸聯動機床和復合加工機床發展空間大。
5.3 數控系統發展趨勢
作為模具制造技術不可缺少的數控系統也朝著良好的方向發展,主要分為以下2個方面。
(1)數控系統向智能化、開放式、網絡化方向發展。數控設備將具有更加智能的系統,如:使用時加工過程自適應控制、自動生成工藝參數等技術,提高零件加工效率和加工質量;采用前饋控制、自動識別負載、自動選定模型、自整定、電機參數的自適應運算等技術,提高系統驅動性能;利用智能化的自動編程、智能化的人機界面,提高系統編程效
率和簡化操作;還有智能診斷、智能監控方面的內容、方便系統的診斷及維修等。
(2)重視新技術標準、規范的建立。目前,美國、日本、歐盟等國家已相繼進行開放式結構數控系統規范(OMAC、OSACA、OSEC)的研究和制定。美國、日本、歐盟作為世界上的三大經濟體系,對數控系統進行了相似的科學計劃和規范的制定,預示著數控技術將迎來重要的變革。為了跟上先進數控技術的發展,中國也開始進行ONC數控系統的規范框架的研究和制定。數控技術誕生后的 50 年內都是采用G、M代碼描述加工過程,這種面向加工過程的ISO6983標準已經不能滿足現代數控技術的高速發展。現在國際上正在研究和制定一種新的數控系統標準 ISO14649(STEP-NC)。新的技術標準將能提供一種具有普遍適用性的中性機制,使同一個數據模型貫穿模具產品的設計、制造、分析、維修
等環節,從而實現整個制造過程乃至各個工業領域產品信息的標準化。
6 、結束語
基于模具制造技術的研究,總結了模具制造技術的相關技術及發展現狀,最后指出了模具制造技術的發展趨勢。
(1)模具加工制造技術,主要包括特種加工、數控加工、柔性制造和快速制模等技術。
(2)模具制造過程中,涉及到的軟件有 2 類:CAM 軟件、模具生產管理類軟件。
(3)常見的模具夾具品牌有 3R 夾具、米思米夾具、Hainbuch夾具、Roehm夾具、EROWA夾具等。
(4)模具制造用到的機床主要有數控銑床、數控車床、加工中心、電火花、線切割、磨床、鋸床、鉆床、激光加工設備等。為了適應模具行業的快速發展,模具 CAM、模具加工設備和數控系統都將朝著智能化、網絡化、高精度和高效率的方向發展。
投稿箱:
如果您有機床行業、企業相關新聞稿件發表,或進行資訊合作,歡迎聯系本網編輯部, 郵箱:skjcsc@vip.sina.com
如果您有機床行業、企業相關新聞稿件發表,或進行資訊合作,歡迎聯系本網編輯部, 郵箱:skjcsc@vip.sina.com
更多相關信息