基于 HNC-8 數控系統的機床熱誤差補償方法
2018-8-8 來源:轉載 作者: 陳國華,閆茂松,向華,李強,張少博,童
摘要: 熱誤差在機床總誤差源中占了極大比重,研究熱誤差補償方法對于提高機床加工精度具有十分重要的意義。基于 HNC-8 ( 華中 8 型) 數控系統的開放性特性,根據機床熱誤差的補償原理,分析熱誤差補償值的計算方法,并據此算法開發了集成于 HNC-8 數控系統的熱誤差補償模塊,最后結合實例,驗證了補償方法的有效性。
關鍵詞: HNC-8 系統; 機床; 熱誤差; 補償方法
數控機床隨著機床定位精度和刀具性能的不斷提高,幾何誤差和切削力誤差在一定程度上已經得到了較好的解決,而溫度變化引起的熱誤差在總誤差源中占了極大比重,成為了影響機床精度、精度保持性的最重要和最難以解決的因素。
減小熱誤差的方法主要有 3 種: 溫度控制、熱穩定性設計和熱誤差補償。溫度控制不易實現,因為溫控總是滯后于溫升,只有發生了溫度變化后,控制機構才會發生作用。熱穩定性設計通常稱為誤差防止法或硬技術,因為它在機床設計制造階段就進行熱誤差機制分析,包括機床溫度場和變形位移場,進而采取結構優化和材料改進等來提高機床的熱穩定性。而熱誤差補償則不需要改變機床結構設計,采用補償控制器加上軟件編程來消除機床自身產生的熱誤差,所以又稱為控制熱誤差的軟技術,被認為是最有效、最經濟的方法。
從目前來看,補償運動控制的實現方法有: (1)通過修改 G 代碼來實施補償,很明顯,該方法實時性差,應用極不方便; ( 2) 開放式數控系統補償法,但國外數控系統完全不開放; ( 3) 數控系統內部參數調整補償法,如螺距補償、齒隙補償、刀補等,但僅靜態補償; ( 4) 原點偏移補償法,但受限于數控系統。
由于以上原因,特別是受限于國外數控系統功能接口的不開放,使得誤差補償技術應用不到位,因此,作者基于 HNC-8 數控系統的開放性特征,根據機床熱誤差補償原理與方法,將熱誤差補償模塊集成于數控系統,以提高機床的加工精度為目的,從而實現擴大國產數控系統的功能。
1 、機床熱誤差補償方法
1. 1 補償原理
機床熱誤差不僅僅與溫度相關,而且與機床的位置有關。為了實現機床熱誤差補償,必須測量指定溫度條件 T 下機床各運動軸在行程范圍內的誤差值序列,并根據誤差值序列運用回歸擬合的方法繪制熱誤差曲線。熱誤差曲線如圖 1 所示。
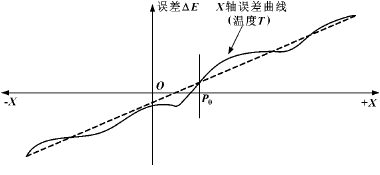
圖 1 X 軸熱誤差曲線擬合圖
從圖 1 可以看出: 在滿足一定精度要求的前提下熱誤差曲線可以用一條直線 ( 虛線) 代替,該直線可以通過斜率與補償參考點 P0唯一確定,這為熱誤差在數控系統中的補償提供了極大方便。只要確定不同溫度下的熱誤差與機床位置的函數斜率及參考點截距,就可以在數控系統中實施動態補償。
1. 2 補償值的計算
對機床熱誤差的補償其實就是對擬合直線的斜率和擬合直線的偏置值進行補償,使補償后的擬合直線斜率為 0,擬合直線偏置值為 0。圖 2 形象表達了補償值的計算方法。以 X 軸補償為例,補償值 Cx由當前指令坐標值Px以及溫度傳感器測量得到的溫度值 T 確定,計算公式如下:

各參數含義如圖 2 所示,具體如下: Cx為 X 軸在 Px位置的溫度補償值; ΔEx為 X 軸在溫度 T 時的熱誤差值; K0為 X 軸位置無關式熱誤差補償值; Px為 X 軸指令位置; P0為 X 軸補償參考點; tanβ 為 X軸位置相關式熱誤差補償系數 ( 即 X 軸熱誤差擬合直線的斜率) 。
1. 3 熱誤差補償插補方法
熱誤差曲線僅描述了針對某一特定溫度的瞬時狀態,所以當溫度變化時補償參數必須根據新的熱誤差曲線重新生成,并傳送給數控系統。熱誤差補償在插補周期內進行,即所謂的插補后補償。為防止機床過載,在按照公式 ( 1) 計算得到熱誤差補償值后,必須先通過監控程序與補償值平滑處理限制補償值的大小,再將其與插補輸出指令位置進行疊加。熱誤差補償插補方法如圖 3 所示。
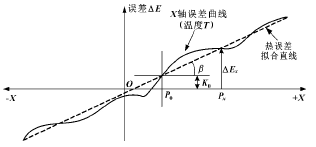
圖 2 誤差補償值的計算原理
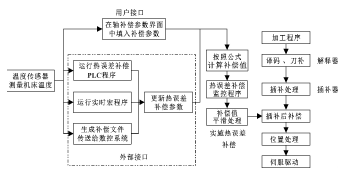
圖 3 熱誤差補償插補方法
1. 4 熱誤差補償模塊開發
基于 HNC-8 數控系統的開放性特性,根據機床熱誤差補償方法,開發了一套集成在華中 8 型數控系統中的熱誤差補償模塊,有效地擴展了國產數控系統的功能以及適用范圍。熱誤差補償模塊如圖 4 所示,主要補償參數有: 補償軸軸號,熱誤差補償類型,熱誤差補償參考點坐標,偏置表起始溫度,偏置表溫度點數,偏置表溫度間隔,偏置表傳感器編號,偏置表起始參數號,斜率表起始溫度,斜率表溫度點數,斜率表溫度間隔,斜率表傳感器編號,斜率表起始參數號,補償率。
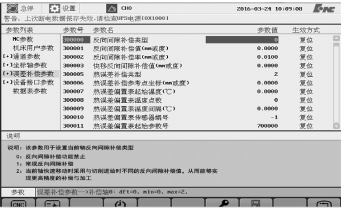
圖 4 機床熱誤差補償模塊界面
2、 實例應用
2. 1 研究對象
以立式加工中心 XHK715 為研究對象,如圖 5 所示。XHK715 配有華中 8 型數控系統 HNC-818B,并集成了機床溫度數據采集系統,該溫度采集系統是基于華中 8 型數控系統設計的對機床溫度信息進行實時采集并實時顯示的溫度檢測系統。通過埋在機床熱關鍵點的溫度傳感器采集溫度信息,并將溫度信息經過HIO 傳輸到數控系統,并在時域示波器界面進行實時顯示。幾何精度測量儀器采用美國 API 公司研發的6D 激光干涉儀。機床的熱變形規律和機床上許多重要部件的溫度變化有關。因此,必須在機床上布置一些溫度測量點來檢定機床的整體溫度,通過對溫度數據進行分析和計算,在機床上篩選出能夠與機床熱變形有較高相關度的溫度測量點,并采集這些溫度測量點處的溫度數據用于機床熱誤差的模型建立。綜合考慮,此次應用驗證以絲杠溫度傳感器的布置點選擇在近電機端的軸承座上為熱誤差建模。
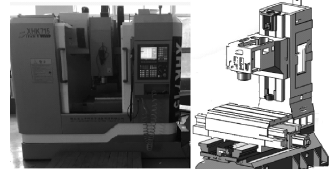
圖 5 研究對象 XHK715
2. 2 熱實驗方案
實驗的目的是對 XHK715 機床熱誤差進行測量與補償,探討溫度對機床 21 項誤差的影響規律,研究華中 8 型數控系統熱誤差補償技術在機床 X 軸絲杠熱誤差補償上的實際適用性。機床空載運行,X 軸以一定進給速度做往復運動,使機床溫度不斷升高,每到溫度間隔點采集一次誤差數據。機 床 誤 差 測 量 與 補 償 實 驗 的 具 體 步 驟如下:
(1) 安裝激光干涉儀。在移動軸運動升溫前安裝激光干涉儀,達到一定溫度時可以直接測量移動軸誤差,機床溫度下降影響測量結果。
(2) 采集機床熱誤差。機床空載運行,X 軸以最大的進給速度 6 000 mm/min 做往復運動,使機床溫度不斷升高,每隔 1 ℃ 測量一次機床誤差。
(3) 熱誤差補償前后對比分析。通過對熱誤差補償前后的對比分析,驗證熱誤差補償方法的效果。
2. 3 補償效果對比分析
由于季節性的原因,車間環境溫度在 18 ℃ 左右,故選取機床誤差測量的溫度區間為 18 ~ 28 ℃ ,溫度間隔取 1 ℃ 。在不同溫度點對機床 X 軸定位誤差進行多次采樣,采樣過程中,由于測量時間長,機床溫度會有 0. 1 ℃ 左右的下降,在處理測量數據時忽略微小溫降。最后對所有誤差數據進行匯總分析,分析結果如圖 6 所示。
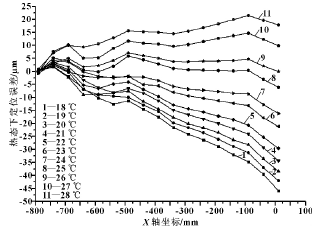
圖 6 X 軸補償前熱誤差曲線
根據 X 軸熱態下的定位誤差統計數據,可以計算出機床熱誤差補償參考點坐標為-800 mm,根據各溫度下的誤差曲線求出各自的熱誤差擬合直線的斜率和在參考點處的偏置值,并以此在 HNC-8 數控系統中設置熱誤差補償參數值,進行熱誤差補償后得到誤差曲線如圖 7 所示。

圖 7 X 軸補償后熱誤差曲線
可以看出: 補償前,在 18 ℃ 時,定位誤差最大值為-47 μm,在 28 ℃ 時,定位誤差最大值為 23 μm。溫度相差 10 ℃ ,定位誤差相差了 80 μm,可見溫度對機床的定位誤差有很大的影響。補償后,不同溫度條件下的誤差曲線基本重合,誤差在 - 3 ~ 5 μm之間。采取同樣的方法,對 X 軸水平方向直線度和垂直度方向直線度進行了熱誤差實驗與補償效果驗證。水平方向直線度,補償前: 18 ℃ 最大值為-15 μm,28 ℃ 最大值達到 25 μm,補償后: 誤差在 - 4 ~ 4 μm之間; 垂直方向直線度,補償前: 18 ℃ 最大值為 17μm,28 ℃ 最大值達到 41 μm,補償后: 誤差在 - 3 ~4 μm之間,熱誤差補償效果顯著。
3、 結論
基于 HNC-8 數控系統的開放性平臺,根據機床熱誤差補償原理,分析了誤差補償值的計算方法,開發了集成于數控系統的機床熱誤差補償模塊,并以一機床 X 軸熱誤差補償為例,進行了應用驗證,補償效果顯著,證明了補償方法的有效性。
來源:湖北文理學院機械與汽車工程學院,襄陽華中科技大學先進制造工程研究院,中鐵十一局集團第一工程有限公司
投稿箱:
如果您有機床行業、企業相關新聞稿件發表,或進行資訊合作,歡迎聯系本網編輯部, 郵箱:skjcsc@vip.sina.com
如果您有機床行業、企業相關新聞稿件發表,或進行資訊合作,歡迎聯系本網編輯部, 郵箱:skjcsc@vip.sina.com
更多相關信息