龍門加工中心絲杠組件熱態性能與溫度場實驗研究
2016-3-14 來源:四川理工學院 機械工程學院 作者:楊海栗 田建平 胡勇 付磊 張良棟
摘要:龍門加工中心絲杠熱變形是影響機床加工精度的重要因素。為減小絲杠熱變形對機床加工精度的影響,以絲杠的實際工況為基礎,建立了絲杠溫度場及熱 - 結構耦合分析模型,運用有限元分析法獲得了絲杠表面的溫度場分布及絲杠重力和進給方向的熱變形規律。運用 M7500 紅外攝像儀進行了絲杠溫度場實驗,驗證了一定時間段內溫度場分析的準確性,并結合實驗對仿真參數進行修正,提高了溫度場仿真分析的準確性,為絲杠進給過程中控制系統的熱誤差補償和整機潤滑散熱系統的結構改進提供了理論依據。
關鍵詞:龍門加工中心;絲杠;溫度場;熱變形;溫度場實驗
0 引言
在精密加工中,機床熱變形所造成的熱誤差是影響機床加工精度的重要因素。滾珠絲杠是其中重要的精密傳動部件,其熱變形將直接影響機床進給方向的加工精度。因此,減少絲杠熱變形所造成的誤差,并在傳動過程中進行熱誤差補償是提高機床加工精度的關鍵所在。
本文以四川某公司 GMC1600A 龍門加工中心 Y向滾珠絲杠傳動系統為研究對象,結合其實際工況,建立絲杠分析模型,并將絲杠螺母對絲杠的作用等效為移動熱載荷及移動力載荷,進行溫度場及熱- 結構耦合分析研究,得到絲杠表面的溫度場分布及熱變形規律,并結合溫度場實驗對仿真分析參數進行修正,提高了溫度場仿真分析的準確性,為絲杠進給過程中控制系統的熱誤差補償和整機潤滑散熱系統結構的改進提供了理論依據。
1 Y 向絲杠傳動系統模型
本文針對該型號龍門加工中心 Y 向滾珠絲杠傳動系統建立分析模型,其三維模型如圖1 所示。結合該加工中心的實際工況,考慮以常用進給速度 8000mm/min 來進行分析研究。該絲杠傳動系統的運動采用螺母旋轉而絲杠固定方式進行,絲杠螺母自身旋轉并帶動十字滑座及其上部件沿軸向移動。絲杠螺母轉動慣性小,易于實現高轉速運動。
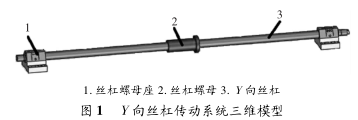
1.1 滾珠絲杠傳動系統的熱力學模型
(1)邊界條件與發熱量計算
滾珠絲杠系統的熱源主要來自于絲杠螺母的循環移動摩擦生熱和兩端軸承的旋轉摩擦生熱。絲杠與外界的熱交換主要為絲杠表面與周圍空氣間的熱交換。滾珠絲杠螺母的熱生成率計算

式中: Q1為滾珠絲杠螺母單位時間產熱量,W ; M 為滾珠絲杠螺母的摩擦力矩,N·m; n 為滾珠絲杠螺母轉速,r/min。
軸承熱生成率的計算:

式中: Q2為軸承單位時間產熱量, W; M 為軸承的摩擦力矩,N·m; n 為軸承的轉速,r/min。對流換熱系數的計算:
絲杠傳動系統與空氣間的對流換熱問題,可采用大空間自然對流換熱關系式

式中: α 為對流換熱系數,W/m2·K; d 為管壁直徑:m; λ 為導熱系數, W/m·K; Nu 為努謝爾特數。
考慮滾動軸承、絲杠及絲杠螺母上的熱量分配,并假設三者間的接觸為面接觸,計算所得參數如表 1 所示。
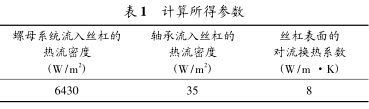
(2)溫度場基本方程
由于絲杠的熱載荷為軸對稱形式,且無內熱源。
假設導熱系數是常數,且滿足圓柱坐標系下的導熱程

其中 2為拉普拉斯算符。在圓柱坐標系中,2T 的形式為: 

其中 α = k/ρc; ρ 是密度,單位為 kg/m3; c 為比熱容,單位為 J/(kg·K); T 為瞬態溫度,r、i、z 為空間變量。
(3)熱變形的基本方程
對于絲杠溫度分布不均的情況, 熱變形滿足下列公式

式中: α 為線膨脹系數; l 為絲杠的長度,m; T(x) 為絲杠溫度分布函數; Δx 為絲杠的伸長量,m。
2 絲杠溫度場及熱- 結構耦合分析
2.1 模型的簡化
該絲杠傳動系統結構并不復雜,但考慮絲杠螺紋節距較小及絲杠螺母在絲杠上的循環往復運動,如在ANSYS 中進行螺紋繪制并網格劃分會造成網格過密及運算量急劇增大的現象。因此,對螺紋部分進行省略,在分析中將絲杠與絲杠螺母的接觸簡化為面接觸;絲杠螺母及軸承對絲杠的作用在溫度場及熱- 結構耦合分析中以載荷的形式進行加載,從而在分析時可對絲杠螺母、軸承及絲杠兩端螺母座進行忽略, 只針對絲杠本身進行分析研究。
在 ANSYS 中進行絲杠建模以后,采用三維十節點熱實體單元 SOLID 90 進行自由網格劃分,為更精確地模擬絲杠螺母在絲杠上的往復運動及觀察各節點的溫度、位移變化,對各邊線和絲杠表面進行了網格細化,劃分單元后單元總數為 37686 個,模型網格劃分結果見圖 2。分析絲杠材料采用軸承鋼,其參數見表 2。
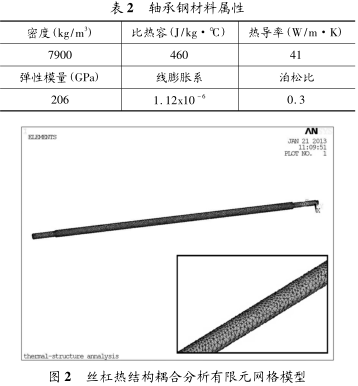
2.2 模型加載
(1)溫度場分析模型加載
在施加移動循環熱載荷的過程中,絲杠初始溫度與外界環境溫度均設置為 20℃,并采用載荷子步的方法模擬絲杠隨時間的溫度變化情況,熱源均以熱流密度的形式加載。在求解過程中,假設絲杠與空氣的對流換熱系數、絲杠螺母和軸承對絲杠的熱流密度均保持不變,熱邊界條件的加載過程如下:
① 由 Y 向進給速度計算出移動熱源的加載速度,同時設定每個載荷步的移動距離和加載時間長短;并計算絲杠與空氣間的對流熱載荷及軸承傳熱。
② 采用 ANSYS 中* DO 與* IF 命令流實現熱載荷的移動及往復運動。因 ANSYS 僅讀取最后施加的面載荷進行計算,因此在熱流加載過程中,每移動一步都需在熱源所達表面施加熱源載荷,并在完成該次運算后將其刪除,同時加載該表面與空氣的對流載荷。
(2)熱- 結構耦合分析模型加載
由于該 Y 向絲杠在運動過程中會受到重力的作用,而絲杠螺母連接在十字滑座上,在其連接處會受到一方向向上的支撐力的作用,分析同時考慮兩載荷作用,從而更為準確的描述了絲杠的實際變形情況。結構分析邊界條件加載過程如下:
①對絲杠的兩端進行全約束,并加載重力加速度;
②采用* DO 與* IF 命令流實現集中力載荷的移動及往復運動,每次循環中需讀取對應時間點的溫度場分析結果;
③在移動力的加載過程中,每移動一步都要在受力絲桿表面形成剛性區域并施加集中力載荷,完成該次運算后,刪掉已施加的集中力載荷與剛性區域。
2.3 計算結果分析
(1)溫度場結果分析
針對本次研究的絲杠傳熱系統,考慮傳動速度及熱載荷加載時間長短,對絲杠螺母 12 次循環后絲杠表面溫度分布進行分析。為更直接的了解絲杠表面的溫度分布情況,沿絲杠表面軸向每隔 50mm 取點,得到其溫度分布。由圖 3 可以發現,絲杠的工作溫度梯度較為明顯,軸承支撐處及絲杠中段有較大溫升,絲杠工作部分溫度基本趨于一致,但出現局部溫度較高點,最高溫度值達 25.53℃,這是由于絲桿螺母正好移動到該處所致;同時可以發現絲杠中部的溫度在一定范圍內出現小幅波動,這是由于絲杠表面移動熱載荷的經過所造成的散熱不均勻現象。絲杠左右兩端的溫度變化趨勢相近,但不完全相同,這是絲杠兩端的結構差異所造成的。
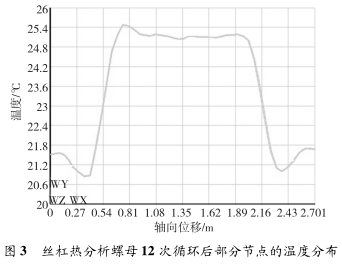
為了觀察絲杠上某節點的溫度變化趨勢,在絲杠中部取一節點,得到該點隨時間變化的溫度曲線,如圖4 所示由圖可知,該點的溫度整體成上升趨勢,但每次循環期間會出現波動,其原因在于移動熱源的往復運動。這一節點在一定程度上反應了前12 次循環工作區域各點的溫度變化趨勢。
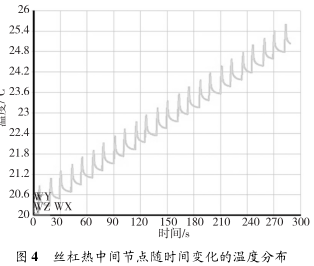
(2)熱- 結構耦合結果分析
在溫度場分析的基礎上進行熱- 結構耦合分析,考慮重力及絲杠螺母的支撐力作用,得到絲杠螺母往復循環12 次后絲杠表面的各節點的位移情況。本文沿絲杠表面軸向每隔50mm 取點,得到絲杠螺母往復循環 4、8、12 次及靜力情況下,絲杠螺母處于絲杠中部時,絲杠軸向及重力方向的位移結果如圖 5、圖 6 所示。由圖 5 可知,軸向最大變形發生在絲杠工作行程靠近兩端處,循環12 次后螺母運動到絲杠中部時絲杠的最大伸長量約為15μm。隨著循環次數的增加,絲杠軸向熱變形的增長趨勢較快,變形量也逐漸增大,最大值均出現在絲杠工作行程靠近兩端處,相較于靜力情況,12 次循環后軸向最大位移處位移增加 11.3μm,相對變化量較大。其變形原因主要為:絲杠的安裝方式為兩端固定,同時受到了重力和十字滑座對其豎直向上的支撐力作用。
當絲杠螺母運動到絲杠中部時,絲杠表面溫度近似對稱分布,熱力學零點出現在靠近中點處,變形量為零。當絲杠螺母移動到不同的位置時,其熱力學零點是在不斷變化的。同時發現,絲杠在熱變形最大點處易產生不均勻變化,對機床的進給傳動精度和穩定性有不利影響,加工時應盡量在絲杠中部進行加工。

由圖 6 可以發現,重力方向的最大變形發生在絲杠中部,12 次循環后,其最大伸長量為 86.2 μm,變形量較大。相較于靜力情況,12 次循環后重力方向最大位移處位移增加 10.4μm,相對變化量較大。對于實際的絲桿安裝過程中已加載預緊力的情況,其形變量會小于分析值,但其相對的變化量依然存在,最終影響重力方向的傳動精度。
由分析結果可以看出,在發熱區域適當增加油冷;加工時避開軸向變形較大處;將所得到的軸向及重力方向的熱變形趨勢和規律引入控制系統,從而為控制系統的誤差補償提供數據支持,是提升整機加工精度的關鍵所在。
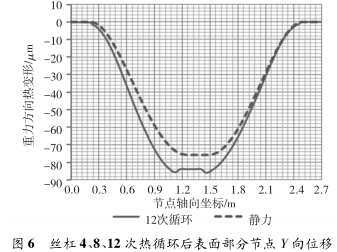
3 絲杠熱態性能實驗研究
在實際加工中,為使機床的熱變形趨于穩定,常需花費較多時間進行預熱,降低了機床生產效率。本文運用米克朗 M7500 紅外攝像儀進行絲杠溫度場實驗,將 ANSYS 模擬值與實際的溫度測量結果進行對比分析,修正理論模擬數據,從而為機床控制系統在加工時進行補償和結構優化提供更具實際價值的理論依據。
由于課題所分析的加工中心在該公司中沒有實體可用于溫度場實驗, 因此本次實驗采用該公司提供的另一型號數控機床進行 Y 向絲杠的溫度場實時測量。
3.1 溫度場實驗
實驗在恒溫 20℃環境下進行,機床 Y 軸以 8000mm/min 的進給速度運行,測量機床從啟動到絲杠表面達到熱平衡時的溫度變化情況,測量循環次數為400 次,并進行多次重復實驗。溫度場測量系統的軟件控制流程及測量現場如圖 7、圖 8 所示。
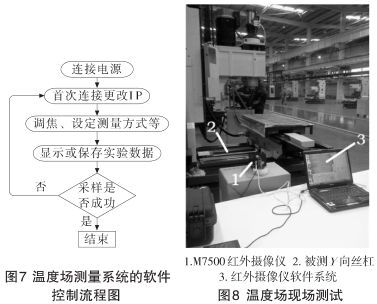
3.2 實驗與仿真結果數據對比分析
由于溫度實驗的絲杠與課題分析絲杠不同,因此按前述相同方法對實測絲杠進行了模擬分析,用于實驗參數對比。
由圖 9 可以發現,經絲杠螺母 365 次循環后,絲杠中部溫度較高,兩端較低,與仿真溫度分布情況類似;在絲杠中部取點,該點溫度場仿真與實測結果對比曲線圖如圖 10 所示。由實測溫度場曲線不難發現,前200s 溫度上升較快,200s 后溫度的增長速度逐漸減緩,最后在 31℃左右徘徊。由實測溫度平均值與模擬值對比可以發現,前 120s 的曲線溫升趨勢相近,絲杠中部一點的仿真與實際測量值在絲杠螺母 12 次循環后分別為 25.8℃與 25℃,溫度偏差小于 0.032%,該分析結果基本符合實際,一定程度上的驗證了前溫度場分析結論的準確性。
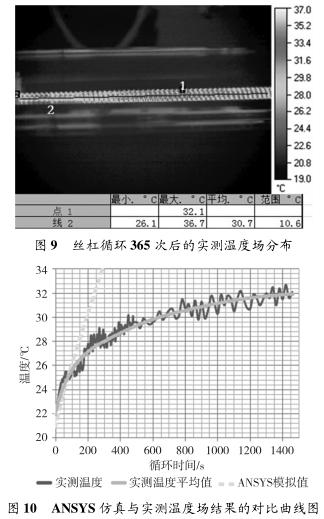
但隨著循環次數的增加仿真分析數值幾乎成直線上升的趨勢,與實際溫度開始趨于平緩的狀況有很大偏差。分析發現造成這一結果原因在于:分析中假設熱流密度與對流換熱系數保持不變,而實際情況下隨絲桿溫度升高,空氣對流加劇,在恒溫環境下,對流換熱系數將不斷增大;絲杠螺母帶動工作臺移動,也其加劇了空氣流動,使換熱速率增大;絲杠表面的溫升使通過絲杠螺母傳入絲杠的熱量減小,熱流密度降低,當絲杠表面熱量的流入與流出達動態平衡狀態時,絲杠溫度趨于穩定,即實驗狀態。只有隨著溫升改變相應仿真分析的熱邊界條件,才能最終使分析結果與實際相符。
3.3 方案改進與結果對比
將絲杠螺母的熱流密度和對流換熱系數都設置為隨溫度而變化的數值,前 40 次絲杠螺母循環的溫度邊界條件的設定如表 3 所示。
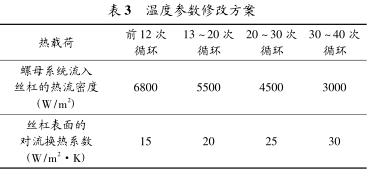
修改方案后,絲杠中部一點隨時間變化的溫度場仿真結果與實測溫度場結果的對比曲線圖如圖 11 所示,圖中不難發現前 320s 的溫度分布與實測溫度變化趨勢相近,各點的溫度誤差不超過 0.05%,很好的模擬了絲杠溫度場隨時間變化的規律,為后續的熱變形分析提供了更為準確的溫度場理論數值。
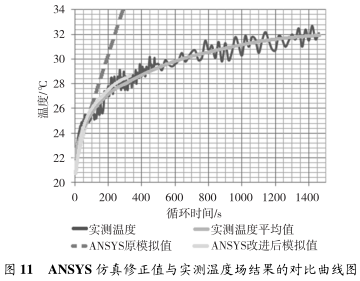
4 結論
本文為了解絲杠組件的熱態性能對整機加工精度的影響,進行了 Y 向絲杠傳動系統的熱- 結構耦合分析。在前人的基礎上考慮了重力及絲杠螺母對絲杠的支持力作用,同時在廠區進行了該結構的溫度實驗,最終得出以下結論:
(1)對 Y 向絲杠傳動系統進行熱- 結構耦合分析發現:在同時考慮移動熱源、重力、螺母對絲桿支撐力作用的情況下,根據實際工況,施加不同循環次數的移動熱載荷后,絲杠軸向位移變化量較小,重力方向位移變化量較大。但相較于無熱源的情況其相對變化量均超過10μm,直接影響了該向加工精度值,因此改善散熱和潤滑條件、集中于絲杠中部進行加工、根據分析結果運用控制系統進行熱誤差補償是減小絲杠熱變形對加工精度影響的關鍵所在。
(2)對絲杠進行溫度實驗,將其與仿真計算結果對比分析,驗證了部分溫度場分析的合理性,同時也發現不足,并對分析邊界條件進行改進,得到更為符合實際的理論分析結果,為企業高速高精度數控機床的溫度補償提供了可行的理論依據。
參考文獻:略
投稿箱:
如果您有機床行業、企業相關新聞稿件發表,或進行資訊合作,歡迎聯系本網編輯部, 郵箱:skjcsc@vip.sina.com
如果您有機床行業、企業相關新聞稿件發表,或進行資訊合作,歡迎聯系本網編輯部, 郵箱:skjcsc@vip.sina.com
更多相關信息