加工中心工作臺結構優化及可靠性分析
2019-2-27 來源:昆明理工大學 沈機集團昆明機床 作者:劉欣瑋 張曉龍 嚴江云 等
摘 要: 針對目前加工中心工作臺在工作時,由于振動和變形產生剛度降低的問題,提出了一種結構優化方案,以驗證優化后工作臺剛度的可靠性。采用有限元法,在靜力學分析的基礎上對工作臺進行了不增加質量而提高剛度的優化; 采用靈敏度分析法對優化后工作臺的剛度可靠性進行分析; 在 six sigma 分析系統中驗證了優化后工作臺的剛度可靠度。分析結果表明: 優化后工作臺的剛度提高 11. 5% ,且可靠度達到 100% ,其中彈性模量及工作臺圓形筋板厚度的隨機變化對工作臺剛度影響較大。該方案能提高加工中心工作臺的剛度并且能確保其剛度可靠性。
關 鍵 詞: 加工中心; 靈敏度分析; 有限元法; six sigma 分析系統
現代機床正在向現代加工中心的方向發展?,F代加工中心轉速可達到 2 000 r/min 以上,快移速度 60m / min 以上并且定位精度不超過 3 μm。這些參數決定了機床必須有更高的剛度。工作臺是機床的重要組成部分,其剛度不僅影響著機床的幾何精度和加工精度,而且影響著機床的加工質量和生產效率。因此,提高工作臺的剛度是提高機床整體可靠性的有效方法。林歡等對工作臺進行了靜動力學分析,對該工作臺進行拓撲優化以提高工作臺系統的固有頻率; 劉光浩等對 ZK5150 型鉆床的工作臺進行有限元靜動態分析,在滿足剛度不下降的前提下對其進行輕量化設計; 楊飛等對立式加工中心的工作臺系統進行模態分析,對其結構進行了改進,提高了各階的固有頻率; 王傳祥等用有限元分析在承受最大載荷時,TH6213 數控鏜銑加工中心工作臺的變形與應力,為驗證機床工作臺設計的合理性與進一步的優化提供了可靠的理論依據。
筆者以上述研究成果為依據,將工作臺的靜剛度作為研究對象,提出了以提高剛度為目標的優化方案。選擇了幾種主要影響參數作為獨立隨機變量,分析各參數的隨機變化對優化后工作臺剛度可靠性的影響,以為提高工作臺剛度可靠性提供參考。
1 、工作臺的優化
1. 1 建模
文中以某公司的 THM46100 高精密臥式加工中心工作臺為研究對象進行建模分析,由于其內部結構較為復雜,建模時對影響較小的微小特征部件進行合理簡化,簡化后的模型如圖 1 所示。工作臺支撐采用轉盤軸承結構,工作時采用液壓夾緊裝置進行夾緊。工作臺的材料為灰鑄鐵 HT250,彈性模量為 113 GPa; 泊松比為 0. 28; 密度為 7 200 kg /m3; 抗拉強度為 240 MPa; 抗壓強度為 820 MPa。工作臺采用自由網格劃分方式,網格劃分模型如圖 2 所示。
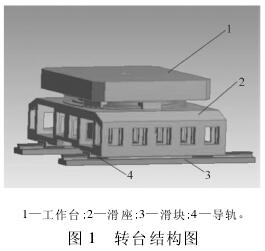
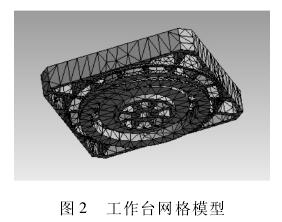
1. 2 有限元模型的驗證
對轉臺進行模態試驗,將試驗的結果與有限元分析的結果相對照,以驗證有限元模型的正確性。被測轉臺采用懸吊的安裝方式以模擬自由狀態,其懸吊頻率為 1 Hz 左右。如圖 3 所示。使用橡皮繩將轉臺吊在剛性較好的支架上,轉臺保持水平。該試驗所采用的測試方式為多點激勵、多點拾振的多輸入、多輸出( MMO) 法。通過試驗與有限元分析,得到了轉臺模態前 6 階的試驗值與計算值,如表 1 所示。
經過計算可以得出,試驗值和計算值之間的誤差小于 10% ,并且振型基本一致。因此,可以證明該建模方法基本正確,該模型可用于后續優化工作。
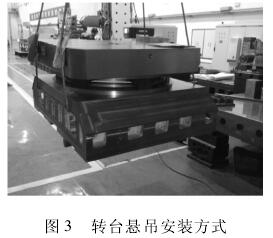
表 1 試驗及計算得到的固有頻率對比

1. 3 工作臺受力與約束分析
1. 3. 1 工作臺受力分析
1) 切削力計算。該加工中心的工作臺自身質量為 887 kg,能承受的最大質量為 3 000 kg。由精密雙導程蝸桿與蝸輪副實現工作臺 360°連續任意分度,蝸桿與交流伺服驅動電機采用進口聯軸器直接連接。下面以工作時最大承力狀況計算切削力 :
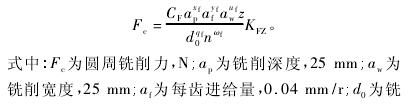
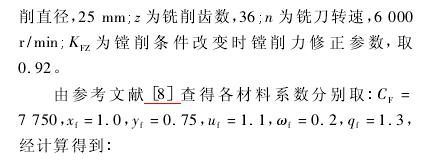
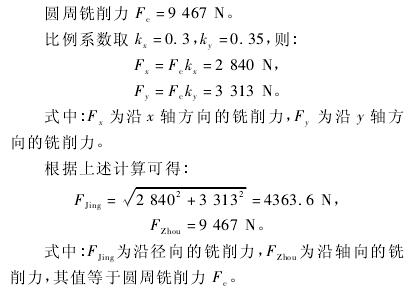
2) 工況下載荷分析及載荷添加加載。工作臺最大的承受質量為 3 000 kg,臺面尺寸 1 000 mm × 1 000mm,取承載面直徑為700 mm,則工作臺承受的面載荷為 P = F /A = 3 000 × 9. 8 /( 3. 14 × 0. 352) = 76 433Pa。為簡化計算,加載時將工件的最大重力均勻地分布在整個臺面上,取有效面進行分析。
由于不能確定加工件高度,因此將切削力作用點沿軸向平移到工作臺面上。工況下液壓夾緊裝置施加夾緊力,經計算為 62 500 N; 根據參考文獻以及廠方提供的預緊力數據,經計算,在 650 N 的預緊力下,軸承剛度為692 N / μm; 最后施加重力。
1. 3. 2 工作臺約束分析
工作臺與轉臺座之間通過軸承相連。軸承承載著工作臺的自重以及加工件的重力。其承載面約束了工作臺的軸向平動,施加此面的軸向位移為零; 承載面( 柱面) 連接軸承內圈,約束工作臺在徑向的來回平動,施加此面的徑向位移為零。
1. 4 結果分析
在 ANSYS Workbench 中,經過全面的計算求解,生成了回轉工作臺的總變形圖,如圖 4 所示。從圖 4可知,工作臺的最大變形量為 y = 64. 2 μm。為了方便計算,根據前文中已計算得出的徑向和軸向切削力,取合外力最大值為 10 000 N 進行計算,得到工作臺部件剛度
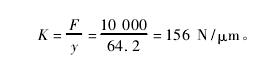
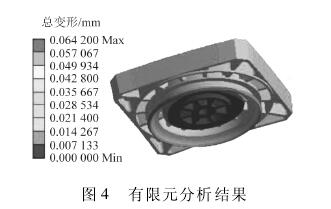
由于工作臺的剛度影響著機床的幾何精度和加工精度,為了進一步提高加工中心的幾何精度和加工精度,應以提高工作臺的剛度為目標進行優化。
1. 5 選擇優化變量
由工作臺的結構可知其圓形筋板的厚度對工作臺剛度的影響較大,因此本次優化主要考慮工作臺上 3個圓形筋板厚度對工作臺剛度的影響。根據工作臺的形狀要求選擇優化設計變量( 筋板內圈直徑 D1,D2,D3) 的取值范圍,如表 2 所示。本次優化設定約束條件為不增加工作臺質量,目標函數為工作臺的最大變形( Max Deformation) 。因為要提高工作臺的剛度,因此須使最大變形量達到最小。
表 2 優化變量取值
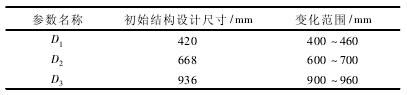
1. 6 優化結果
經過優化,得到了優化后的變量數值以及優化前后的變化對比,如表 3 所示。由表 3 可以看出,設計變量變化最大的為 D2; 優化后工作臺的最大變形量為56. 8 μm,相較優化前減小了 11. 5% ; 優化后工作臺的質量為 887. 84 kg,相較優化前略有增加,但整體影響不大,符合限制質量的約束條件。
由最大變形量可計算得到優化后的工作臺剛度為 176 N/μm。相較優化前 156 N/μm,提高了 11. 5% 。達到了優化目的。
表 3 優化前后變量對比
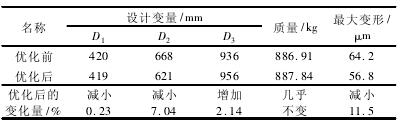
2 、優化后工作臺剛度可靠性分析
2. 1 確定隨機變量
優化后的工作臺在工作時受力有不均勻性,并且主要尺寸參數具有分散性,會對剛度造成影響,因此筆者選取以下主要參數來分析優化后工作臺的剛度可靠性: 材料、軸承剛度、外載荷以及工作臺主要尺寸( 優化后的筋板內圈直徑 DS1,DS2,DS3) 。其中工作臺尺寸參數如圖 5 所示。由參考文獻知,尺寸偏差多服從正態分布,其標準差是允許偏差的 1 /3。
如表 4所示。已知彈性模量、軸承剛度以及外載荷的均值分別為 110 000 MPa、692 N/μm、10 000 N,假設它們都服從正態分布,且取它們的變異系數依次為 0. 04、0. 02、0. 02
,則標準差可由變異系數計算得到,分別為 4 400MPa、13. 84 N / μm 及 200 N。
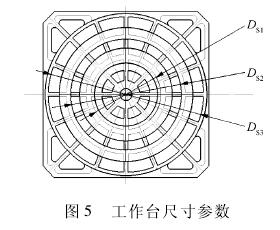
表 4 隨機變量的統計特征
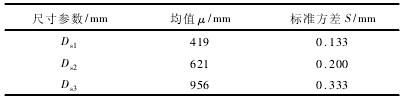
2. 2 可靠性靈敏度分析
可靠性靈敏度分析可以提供某一隨機變量變化引起可靠性的變化率的信息。經過分析,得到隨機變量相對最大變形量的靈敏度關系,如圖 6 所示。在圖6 中,可根據直方圖面積的大小直觀地看出每個變量對最大變形量的影響程度。其中,縱坐標 y = 0 上方的直方圖表示該變量與最大變形量呈正相關,反之,為負相關。
由分析結果可知,這 6 個隨機變量對最大變形量的靈敏性程度由高到低依次為彈性模量、DS1、DS2、DS3、外載荷 F 和軸承剛度。其中彈性模量、DS1、DS2的變化對工作臺剛度影響較大,為靈敏性因素,其他 3 個變量為非靈敏性因素。

2. 3 剛度可靠性分析結果
在 Six sigma 分析系統中,抽樣類型包括蒙特卡洛抽樣法和拉丁超立方抽樣法,由于后者對樣本數量的節省非常顯著,因此選擇拉丁超立方抽樣法進行抽樣。如圖 7 所示,設定程序進行 10 000 次抽樣后可以看到,圖中柱狀圖沒有較大的跳躍或間隙,因此抽樣次數是足夠的。
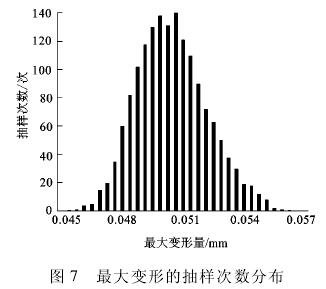
如表 5 所示,在參數概率列表中插入值 0. 060 000mm,得到概率顯示為 1. 000 00,即抽樣分析得到的最大變形量均為小于 0. 060 000 mm,相比優化前的最大變形量 0. 064 200 mm 有了較大改善。優化后工作臺靜剛度可靠度為 100% 。
3 、結論
通過 ANSYS 平臺對加工中心回轉工作臺進行剛度優化以及可靠性分析,得到以下結論:1) 通過靜力學有限元分析對回轉工作臺進行優化,在不增加質量的前提下,使工作臺的剛度提高11. 5% ,對改善加工中心機床幾何精度與加工精度起到了一定效果。
表 5 參數概率列表
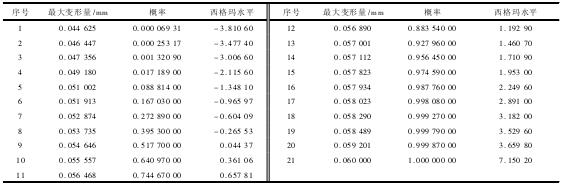
2) 選取參數進行統計處理并將它們作為獨立隨機變量,采用拉丁超立方抽樣方法對優化后的工作臺進行可靠性分析。由靈敏度分析得到影響較大參數,優化后工作臺剛度可靠度為 100%
,安全可靠。
投稿箱:
如果您有機床行業、企業相關新聞稿件發表,或進行資訊合作,歡迎聯系本網編輯部, 郵箱:skjcsc@vip.sina.com
如果您有機床行業、企業相關新聞稿件發表,或進行資訊合作,歡迎聯系本網編輯部, 郵箱:skjcsc@vip.sina.com
更多相關信息