基于試驗模態的精密加工中心動態性能分析
2018-5-14 來源: 大連理工大學 機械工程學院 作者:馬 躍,岳文斌,黃余彬,孫清超,楊帥杰等
摘要: 在對模態測試原理進行分析的基礎之上,通過試驗模態分析法獲取了某型號臥式精密加工中心的固有頻率、模態振型和阻尼比。依據測試結果,結合傳遞函數分析,驗證了被測對象具有良好的低頻動態特性。同時,在將測試結果與加工中心實際使用工況進行對比后,針對影響整機動態性能的工作臺與立柱進行了實際裝配條件下的局部模態測試,依據理論分析和所測結果,對發現的薄弱環節提出了相應的優化設計建議以改進其動態性能。上述工作可為同類型機床的結構優化設計與相關試驗提供一定的參考。
關鍵詞: 振動測試; 動態特性; 模態分析; MIMO; 加工中心
0 引言
數控機床是當今精密加工制造領域的重要設備,其加工精度與加工效率日益受到人們的重視。 加工中心做為一種高度自動化的多功能數控機床,其自身的性能穩定性尤為重要。
在實際加工過程中,振動是影響加工中心性能的一個關鍵因素。
引起機床振動的主要原因包括回轉零部件因質量不平衡引發的受迫振動,以及刀具和工件之間因相對運動引發的自激振動等。
在兩種類型振動的綜合作用下,機床往往會產生繁多而復雜的振動形式,極大的影響其加工性能 。
因此,機床的動態性能已成為其性能評價的重要指標 。對機床動態性能的研究,通常采用計算機模擬仿真與振動試驗兩種方法。
而對諸如機床之類大型結構的模擬仿真,往往離不開振動試驗的支持,如對于機床性能影響較大的結合面 ,其仿真時模型參數一般需要結合實際的試驗給定 。
因此,振動試驗分析方法是研究機床動態性能的重要手段。
它可以驗證仿真分析的準確性,可以評價機床的抗振性能,可以了解機床的薄弱環節,也可以為機床結構優化設計提供重要的參考依據。振動試驗包括結構的固有屬性測試、動力響應測試以及動力穩定性測試。其中固有屬性的測試一般由試驗模態分析完成。
它通過對激勵及響應信號的采集與處理,獲得系統的傳遞函數,然后用一定的擬合方法得到結構的固有頻率、模態振型和阻尼比等模態參數,從而幫助設計人員在預防共振,發現結構薄弱環節和評價減振性能方面提供數據支持 。
本文以試驗模態分析理論為基礎,針對某型號精密臥式加工中心( 下文簡稱測試對象) ,通過多點激勵多點輸出( Multiple Input Multiple Out,MIMO) 模態分析法來獲取整機及局部的固有頻率、模態振型和阻尼比,進而對加工中心進行動態性能分析。1 試驗模態分析原理一個 N自由度的線性定常系統,其運動微分方程為:
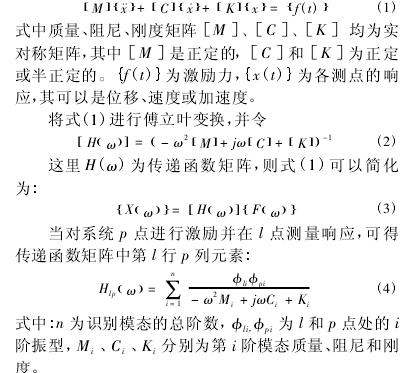
由式( 4) 可知,式( 2) 的一行或一列包含了試驗需要獲得的所有參數。
本文在獲得傳遞函數后,從時域與頻域兩個方面,分別使用特征系統實現算法和復頻域最小二乘法對數據進行擬合處理,即可獲得試驗對象的模態參數。試驗模態分析法包含單點激勵多點輸出( SingleInput Multiple Out,SIMO) 和多點激勵多點輸出 ( MI-MO) 兩種方法,其特點如表 1 所示。
根據二者在四個方面的性能對比,針對大型結構件的模態測試,MIMO具有較大的優勢,故本文選用 MIMO 模態分法。
表 1 SIMO 與 MIMO 特點比較

2 、臥式加工中心模態測試
2. 1 模態測試系統
本文通過構建的模態測試系統,針對重 25t,床身設計剛度良好的某型號精密臥式加工中心進行了模態測試。測試系統由激勵系統,響應信號采集系統及數據存儲與處理系統三部分組成。其中,激勵系統由 YC-3 型高彈性聚能力錘及 1 個 YFF-6 型力傳感器 ( 量 程 為 125k N,靈 敏 度 為4. 17PC / N) 和 YD-1 袖珍型電荷放大器組成( 可對幾百公斤到上百噸的結構進行激勵) ; 考慮到試驗成本,響 應 信 號 采 集 系 統 由 5 個YSV2303 型三向加速度傳感器( 量程為 50g,靈敏度為 100mv/g,頻響范圍為 0. 5 ~5k Hz) 組成; 數據存儲及處理系統由 YSV8116 型智能信號采集儀和 DASP 軟件構成。
圖 1 是被測對象實景圖。
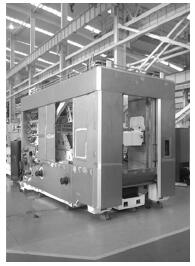
圖 1 被測對象實景圖
2. 2 模態測試方案
在確定模態測試方案時,從測點的布置,測試方向的選取及激勵點的選取 3 個方面進行分析。在測點的布置中,考慮到測試對象的核心結構包括主軸箱,十字滑臺,工作臺,立柱和床身等五大部分,故測點也集中布置在這五大部分上。在測點分布選擇上,充分考慮了該加工中心的幾何尺寸與結構特點,在準確表達振型的情況下盡量簡化測點的布置,對次要結構進行測點簡布,對結合面如床身與立柱結合面進行測點密布,其他部位則進行測點均布。
依據這些原則,共用 227 個測點對整機結構進行測試,各測點分布如圖 2 所示。圖 3 為主軸滑軌局部測點圖。
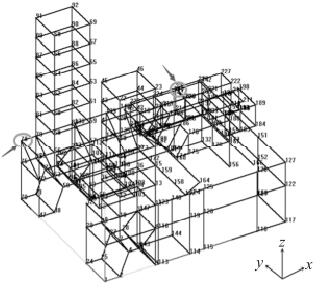
圖 2 各測點分布圖
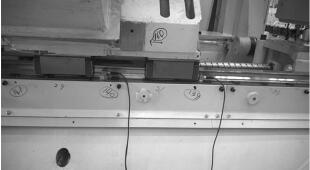
圖 3 主軸滑軌局部測點圖
在測試方向的選取上,依據機械振動理論和對試驗對象的結構分析,確定該加工中心的主要振動方向在 x、y 兩個水平方向上,垂直向受加工中心自身結構和邊界條件限制,其振動響應較其他兩個方向可忽略不計,不作為本文模態測試的關心方向。在激勵點的選擇上,對力錘激勵的試驗模態分析,根據激勵點及響應點位置的不同,可分為單點拾振法和單點激勵法。
對于加工中心等精密加工制造設備,其主軸等部位不允許進行激勵,故本文選用單點激勵法。試驗時分別在立柱和床身上選擇多個點進行試激勵,觀察響應信號的頻譜分布,結合試驗的可操作性,最終確定在立柱 78 點的 X 方向及床身 141 點的 - Y方向進行激勵。激勵點的位置在圖 2 中用圓圈標注。
2 . 3 模態測試過程
模態試驗中,測量信號的獲取是通過傳感器所產生的正比于被測對象加速度的電信號來實現的。傳感器與被測對象的聯接方式包括栓接、粘結以及磁力吸附等多種方式,安裝剛性越好,所測信號的準確度也就越高。
在現場測試時,考慮到機床的結構特點、環境條件、被測對象的表面涂裝面及試驗的可操作性,本文選用絕緣磁座將 YSV2303 加速度傳感器吸附在測點處。測試時,只測量水平 X、Y 兩個方向的振動。227個結構測點由 5 個 YSV2303 三向加速度傳感器和 11個采集通道分成 41 組測完。為了減小因力錘敲擊力度不均引起的測量誤差以及測試噪聲的干擾,每組測點敲擊三次后再進行平均計算。測試對象的最高轉速為 16000rpm,關心的頻率范圍在 300Hz 以內。
為了保證試驗效果,準確的采集激勵及響應信號,本文采用變時基技術,響應信號的分析頻率為 500Hz,力信號的分析頻率為 4k Hz,變時倍數設置為8。在計 算 傳 遞 函 數 ( Frequency Response Function ,FRF) 時,對力信號加力窗,對響應信號加指數窗。測試時,正確的力信號及加速度響應信號如圖 4所示
。
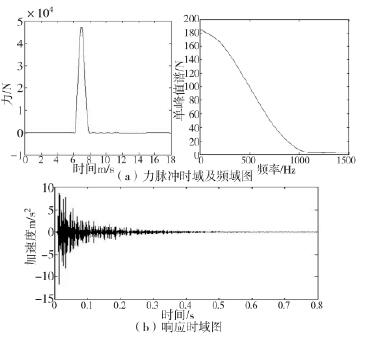
圖 4 激勵及響應信號圖
3 、測試結果及動態特性分析
3. 1 整機模態測試結果分析
通過比較特征系統實現算法和復頻域最小二乘法兩種擬合方法的數據處理結果,本文提取了整機的固有頻率、模態振型和阻尼比。圖 5 為整機模態測試227 個測點的 FRF 在
0 ~ 160Hz 的瀑布圖。表 2 中列出了加工中心前 5 階模態的固有頻率、阻尼比,并對主要振型進行了描述。圖 6 為整機測試得到的 1 ~ 5 階模態振型圖,本文的振型分析基于振型動態圖,由于論文表達形式所限,文中的振型圖均為靜態圖。
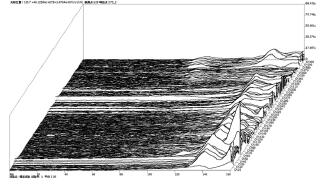
圖 5 整機 FRF 在 0 ~ 160Hz 瀑布圖
通過對瀑布圖的分析可以看出,各測點的 FRF 在80Hz 以下峰值基本為零。另外,針對整機固有頻率進行分析,第一階固有頻率較高,為 87Hz,而類似機床的一階固有頻率一般較低,如史安娜等對某型號數控機床進行模態測試,得到的一階固有頻率在 19. 4Hz。由以上兩點可以確定該加工中心在低頻段的動態性能良好。
分析整機測試各階模態振型,第一階振型為主軸箱獨立的彎曲擺動,這是由主軸箱抗彎曲和抗扭轉變形能力不足以及主軸箱與滑枕連接剛度不足引起的。應從改進主軸箱材料與結構,改變其與滑枕連接方式兩個方面來提高其抗振性能。
而對于后四階整體振型,加工中心的整機同向晃動對加工精度影響較小。但當發生共振時,機床較大的振動不利于加工作業的進行,故應避免轉速檔接近 116Hz 與 139Hz。在 151Hz與 179Hz 附近出現了左右兩立柱之間,工作臺與主軸之間的反向振動,在加工時會引起刀具與工件的相對位移,從而影響加工精度,屬有害模態。
表 2 整機前 5 階模態參數
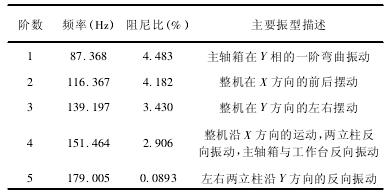
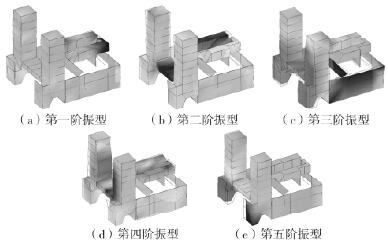
圖 6 整機模態振型
3. 2 局部模態測試與結果分析
通過對整機模態振型的分析可知,在前 5 階振型中床身的變形小,剛度良好,振型主要出現在立柱與工作臺上。這與現場調試人員反應的問題相吻合,即在加工中心實際調試過程中,當刀盤轉動時,立柱會出現顫振,而工作臺也存在著靜不穩定現象,故可以確定工作臺與立柱為整個加工中心的薄弱環節,是影響整機動態特性的關鍵因素。
為了更好的觀察立柱與工作臺的振動特性,分別對二者進行實際裝配條件下的局部模態測試。工作臺的測試結果如圖 7、圖 8和表 3 示,圖中坐標系同前。
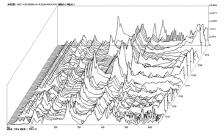
圖 7 工作臺 FRF 瀑布圖
表 3 工作臺局部試驗模態參數
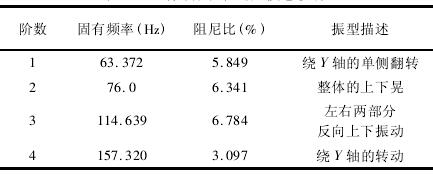
圖 8 工作臺局部模態振型
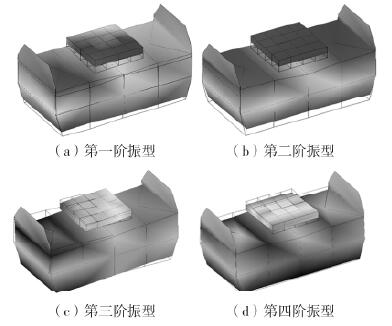
分析工作臺各階模態振型,第一階振型與工作臺的靜不穩定現象相吻合。根據工作臺的結構分析可知,其兩側與立柱的結合分別由 6 個螺栓在四周均布完成,這樣結合面在內部連接剛度較差,易發生變形,建議在結合面內部增加固定螺栓以提高結合面的剛度。
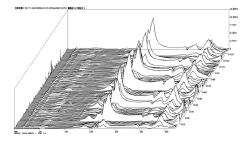
圖 9 立柱 FRF 瀑布圖
圖 9、圖 10 及表 4 為立柱局部模態測試結果。
表 4 立柱局部試驗模態參數
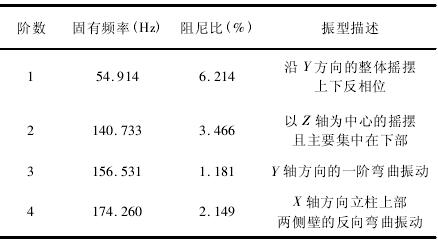
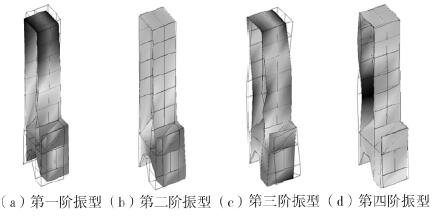
圖 10 立柱局部模態振型
根據立柱的局部模態振型分析,其薄弱環節表現在兩處,一是立柱下部與床身結合面連接強度較低,二是立柱上部兩側面剛度較小。分析其原因,由于床身和立柱在結合面處只由 5 處 M16 內六角螺栓加墊片后進行連接,約束較弱,易發生振動,而對于立柱上部兩側面,其實際結構間由于安裝絲杠而缺少加強結構,易發生變形。
本文建議在結合面處加大連接螺栓的直徑以提高連接強度,在立柱兩側面加入加強筋來改善結構剛度,減小振動變形。
3. 3 整機與局部模態測試結果對比
對于加工中心等大型設備,因其產品特征導致結構復雜,往往會存在大量的結合面。結合面在受到外力后,表現為既有阻尼,又有彈性,既消耗能量,又存儲能量的特性,這會使得模態測試結果發生復雜的變化。
表 5 整機與局部模態測試固有頻率對比
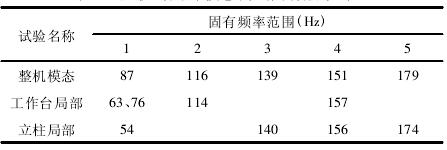
將整機與局部模態測試所得固有頻率按頻率段劃分可得表 5,對其進行分析可知,實測整機一階固有頻率要高于局部的一階固有頻率。由模態分析理論可知,隨著試驗對象質量與結合面數目的增加,整機的固有頻率會降低。但該加工中心床身本身具有良好的剛度,整機質量又達到 25t,激勵能量無法使床身產生較大振幅。
此外,從設計圖紙對結構進行分析可知,立柱與床身處的結合部動態特性差,對能量的消耗大,最終使得某些局部模態難以得到有效激勵。所以整機模態測試并沒有得到某些局部低階模態。
另外,對于加工中心的同一部件,如立柱,在整機與局部的模態測試結果中振型相差較大,難以吻合,其原因主要表現在兩個方面: 首先,由于加工中心整機中存在的大量結合面導致對測試結果影響較大。
整機模態測試數據受全部結合面的影響,得到的立柱振型是所有結合面共同作用的結果,而立柱的局部模態測試結果只受與立柱有關的結合面的影響,排除了其他結合面的干擾; 其次,在進行整機測試時,往往由于激勵能量的不足,某些局部模態并不能有效的激勵出來,而在進行局部模態測試時,激勵點及激勵方向的改變,對振型影響很大。因此,在本次試驗中,整機與局部模態才會出現較大的差異。
通過以上分析可以看出,對于結構復雜的大型設備,其整機模態測試并不能很準確的得到每一個部件本身的動態特性。要想對關鍵部件進行動態特性分析,有必要對其進行實際裝配條件下的局部模態測試。
4 、結論
本文以試驗模態分析理論為基礎,針對某型號精密臥式加工中心,通過 MIMO 模態分析法,獲得了整機及局部的模態參數,并以此為依據進行了加工中心的動態性能分析,完成的研究工作具體包含以下幾個方面:
( 1) 在對試驗模態分析理論研究的基礎之上,利用激勵系統,響應信號采集系統及數據存儲與處理系統三部分搭建了試驗模態測試系統。
( 2) 利用試驗模態測試系統,對整機及局部( 工作臺和立柱) 進行了模態測試,獲取了整機及局部的固有頻率、模態振型和阻尼比。
( 3) 通過整機模態測試結果的分析,驗證了整機具有良好的低頻特性。同時,將測試結果與機床實際使用情況相比較,確定了工作臺與立柱是影響整機動態特性的關鍵因素。據此,在實際裝配條件下對二者進行了局部模態測試。依據測試結果,對發現的薄弱環節提出了相應的優化設計建議以改進其動態性能。
( 4) 通過對比整機與局部的模態測試結果,得出對于結構復雜的大型設備,除進行整機模態分析外,有必要結合實際裝配條件下的局部模態測試,才能更好的分析其動態特性的結論。
投稿箱:
如果您有機床行業、企業相關新聞稿件發表,或進行資訊合作,歡迎聯系本網編輯部, 郵箱:skjcsc@vip.sina.com
如果您有機床行業、企業相關新聞稿件發表,或進行資訊合作,歡迎聯系本網編輯部, 郵箱:skjcsc@vip.sina.com