一種重型液壓油缸加工工藝的研究
2018-5-7 來源:惠州市技師學院 作者: 陳義華
摘要:本文主要介紹一種重型液壓油缸的機械加工工藝。液壓油缸的機械加工其加工質量的好壞直接影響整個油缸的壽命和可靠性,缸筒加工要求高,其內表面粗糙度要求為Ra0.4~0.8μm,對同軸度、耐磨性要求嚴格。缸筒的基本特征是深孔加工,其加工工藝一直困擾著許多機械加工制造人員。
關鍵詞:重型液壓油缸;表面粗糙度;圓柱度
C5112A立式車床,屬工作臺移動式車床,加工特點切削直徑1250mm,車床布局的主要特點是主軸垂直布置,安裝工件的圓形工作臺水平布置,故笨重工作的裝夾、找正比較方便。此外,工件及工作臺的重量均布在工作臺導軌及推力軸承上,大大減輕了主軸及其軸承的載荷,因此,對減少磨損,保證加工精度十分有利,并能長期保持工作精度。所以對加工重型液壓油缸十分有利。圖1為油缸加工圖紙,油缸的加工工藝過程見表1。
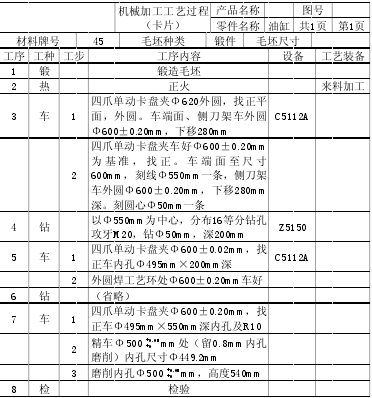
表 1 油缸機械加工工藝過程
一、粗車(如圖1所示的油缸)
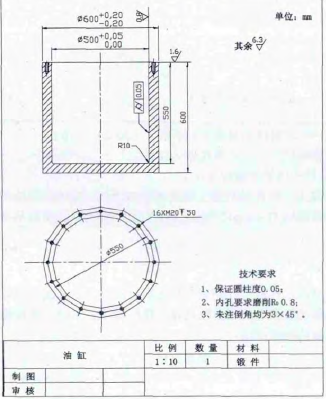
圖1
1.液壓油缸為45鋼材鍛造、并退火(外資企業來料加工)是一個大而重的圓柱體工件,重約1300kg。工件重而不規則圓,要考慮粗車過程的兩次起重和裝吊工件上下平行和安全,所以設計了焊接三點吊環的工藝,如圖2所示。
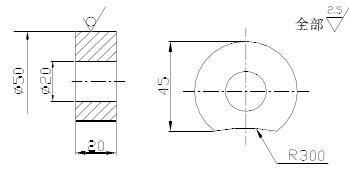
圖2
注:用45鋼材料Φ50下料80mm長,車孔Φ20mm,厚20mm,共3件。銑去5mm外圓尺寸R300mm位(作與油缸外圓毛坯焊接位)。將工件毛坯取總高一半分三等份將3個吊環工藝焊接牢固。如圖3所示工件實樣毛坯。
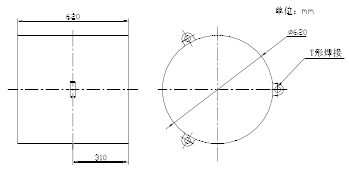
圖3
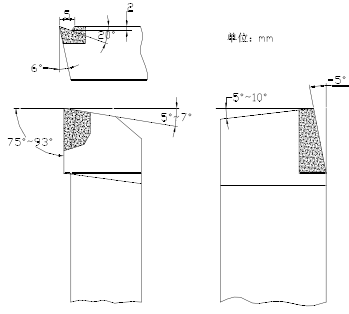
圖4
2.將焊接后的工件用3根圓鋼絲繩拴在3個吊環支承孔中,固定后用吊車輕放在立車工作臺面上,用四爪單動卡盤校正平面、外圓夾緊夾牢。(因工件外圓為毛坯鍛造故不規則圓,所以用4件厚銅板分別放入4個卡爪中支承夾緊工件表面)
3.粗車平面見光,用側刀架將外圓車至尺寸Φ600mm,下移高度280mm,以不碰工藝吊環,倒角3×45°。
4.卸下工件調頭,以已車好的平面和外圓作基準面用四爪單動卡盤校正外圓夾牢工件,并用磁性百分表檢查外圓。按工藝過程3工序車端面取總高600mm,外圓用側刀架車外圓600mm下移280mm,以不碰工藝吊環。在端面上刻圓心Φ550mm鉆孔中心線(16×M20螺紋處用),另以圓心線刻一條Φ50mm鉆孔工藝中心線,倒角3×45°,卸下工件,吊去鉆床上去鉆孔。
5.由于立車不具備鉆孔機構和工裝夾具,所以轉下道工序鉆床引鉆Φ50mm×200mm深的工藝孔。(作立車背吃刀量進給)并在鉆床上將Φ550mm中心線分布16等份M20×50深的螺紋攻好,(也可作吊起工件的工藝螺孔)將原焊接的3個工藝吊環割去,并打磨好。
6.利用工件端面螺孔,用兩個標準的M20吊環旋緊端面對稱中心處,用兩根鋼絲平行工件吊起1m高,擦干凈底面,輕放立車工作臺面上,用四爪單動卡盤將工件校正夾牢。刀具選擇:由于工件內孔加工余量大,切削后工件為1/4的重量,為凹孔Φ500mm×550mm深。針對加工余量大,孔底深,排屑困難等不利因素,我采用合理車刀幾何角度,選用硬質合金為YT5 YT15,主偏角為90°,斷屑槽為外斜式,前寬后窄,前深后淺,刃傾角為負值,易形成切屑C形或6形,斷屑范圍寬,斷屑穩定可靠,如圖4所示。
7.在合理的刀具中粗車由中心背吃刀量ap/8mm向外緣徑向切削,進給量為f/0.5mm切削速度為V=55~75mm/min,將工件車至Φ495mm,留5mm精車。車完每一刀,用垂直刀架下移一刀,由于凹孔越車越深,排屑越難,我采用大型喇叭的鐵芯,(磁鐵)每車一刀停機下來吸一次鐵屑,以免工件之內的鐵屑多而打壞刀具,順利車削深度為200mm。另將原外圓3個工藝處用側刀架車Φ600mm,使外圓為圓柱體。
8.卸下工件吊至鉆床引鉆中心工藝孔Φ50mm×550mm內孔總高,(采用加長深孔鉆削,工藝過程省略)鉆完孔后將工件吊放立車工作臺面上,用四爪單動卡盤找正夾緊。由于工件內孔深為550mm,垂直刀架下移切削將會碰工件,所以特做一把加長刀桿,如圖5所示。刀桿材料選用45鋼并調質,尾部莫氏5號錐柄與垂直旋轉刀架錐孔配合緊固,刀桿做好后,裝入刀架錐孔,并鎖緊刀架上的錐度自鎖裝置螺釘,保證刀桿安裝牢固,切削振動時不會掉刀。因軸小而又長,所以刀具采用90°偏刀、增大前角,刃傾角為正、刀尖圓弧減少,使切削刃鋒利,減少刀桿受力時切削振動。背吃刀量ap/5mm,進給量f/0.3mm,切削速度V55~75m/min,順利將工件車至內孔為Φ495mm,內孔總高為550mm,R10車好。
二、精車
工件粗車好后,重新裝夾校正工件,以免粗車時工件移位或不平,為了磨削最后一道工序做好準備,精車至為重要。因工件內孔圓柱度要求高為/0/0.05mm,為保證圖紙要求,在精車中(因粗車留下5mm)每次背吃刀量1mm車削一次,用內徑千分尺上下測量圓柱度,修正垂直刀架溜板至圓柱度為0.05mm以內。并留0.8mm余量為磨削。
三、缸筒內表面磨削
1.關鍵最后一道工序磨削。工件油缸表面粗糙度為0.8,公差等級IT6級,圓柱度0.05mm,對油缸要求精度高及表面粗糙度高的情況,而且立車轉塔刀架與垂直中滑板為一整體,故不能卸下刀架,需另配裝磨頭夾具。所以既要保證圖紙尺寸要求,又要準時交貨,我采用新型的手動砂輪機,將原電動機后蓋卸下,以主動電機軸前后中心孔為基準,在車床(C6140)上采用前后兩頂針車削電機鋁外殼以圓為基準并留0.5mm為臺階作定位,外圓Φ120-0-0.05mm×100mm。
2.做一個專用夾具電機外殼套。圖6為下料φ140mm×孔φ110mm45號無縫圓鋼管,長100mm。在外圓焊一條30mm×30mm長100mm的四方長鍵作立車刀架裝夾緊作用,φ120的孔在車床上加工完畢。另將電機兩頭前后軸承改換為圓錐滾子軸承GB300200型。外殼專用套車好后將電機外殼整體用油壓機輕壓入夾具套內,并用M12的螺釘緊固電機外殼。改裝后的手動砂輪機變成機械緊固式磨頭,其有效工作深度為580mm,磨頭采用型號為GB/T2476-1994WA(GB)150X30A60的氧化鋁砂輪。其功率0.8k W,三相電壓,采用1.5k W變頻器電子無級調速,調定轉速為1440r/min,如圖7所示。
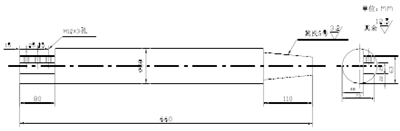
圖5
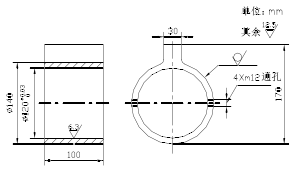
圖 6 專用夾具套
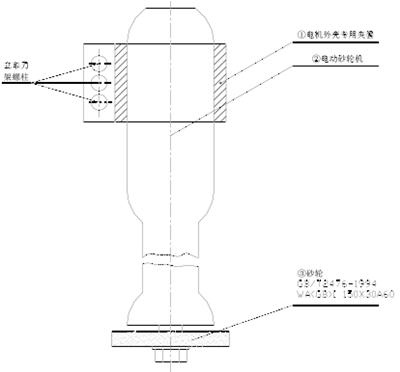
圖7 整體機夾式磨頭
3.油缸磨削工作高度為540mm尺寸,將機夾磨頭安裝在立車刀架上,每次磨削背吃刀量ap/0.05mm,切削速度Vc40m/min,進給量f4mm/r因磨削進給量大而快,所以采用垂直刀架中滑板的刻度尺調整為540mm用白色粉筆標記,以免磨頭砂輪碰到底面。磨削中采用干磨,如磨頭發熱即停下機床來進行風冷卻,在常溫下再磨削,每磨削幾次進給用金剛筆修整砂輪(金剛筆裝在側刀架上緊固)上下修整。
在整個磨削過程中,表面粗糙度已達0.8IT6級,圓柱度0.02mm,內徑Φ500+0.05+0.03mm。經檢驗、各項要求合格達標,使外資企業非常滿意。按以上機械加工方法成功為客戶加工了12個液壓油缸,給企業創造了顯著的經濟效益。
圖7為整體機夾式磨頭。
三、結語
綜上所述,加工大而重的液壓油缸,關鍵要充分利用立式車床的加工原理,合理使用刀具的幾何角度和加工工藝方法,充分理解圖紙的各項要求,即使難度大、精度高的工件都能在設備和技術的突破中解決。
投稿箱:
如果您有機床行業、企業相關新聞稿件發表,或進行資訊合作,歡迎聯系本網編輯部, 郵箱:skjcsc@vip.sina.com
如果您有機床行業、企業相關新聞稿件發表,或進行資訊合作,歡迎聯系本網編輯部, 郵箱:skjcsc@vip.sina.com
更多相關信息