高強度精密螺栓加工方法優化
2019-4-11 來源:中車戚墅堰機車有限公司 作者:劉劍峰
摘 要: 本文主要從設備的合理選擇、刀具的選用、先進加工方法的引進等方面,詳細闡述了高強度精密螺栓的加工方法分析和優化的過程,為類似產品的加工,提供參照辦法。
關鍵詞: 精密螺栓; 優化加工; 斷屑; 車削; 滾壓
1、產品結構特性和技術要求
高強度精密螺栓是某公司加工的主要零部件,其主要特點是:等級高、強度高、精度要求高。下面以典型的高強度精密螺栓—氣缸蓋螺栓(見圖1)為例,分析產品的結構特性及技術要求。
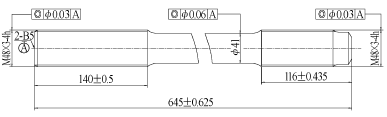
圖1 氣缸蓋螺栓
氣缸蓋螺栓是柴油機上的一個關鍵零部件,其作用是將氣缸蓋牢固地固定在機體上,在柴油機運行過程中承受較大的拉力和扭矩,因此對產品的加工精度要求非常高,主要體現在以下2個方面:
(1) 產品的材料為18Cr2Ni4WA,是一種高強度合金結構鋼,經過調質后有較高的強度和韌性(抗拉強度不小于1 175 MPa,屈服強度不小于1 029MPa,伸長率不小于10%,收縮率不小于45%)。
(2) 產品的加工精度要求高:①產品的形位公差要求較高,其螺栓螺紋及桿身的同軸度要求分別為0.03 mm和0.06 mm;②產品的兩端螺紋等級要求高,均為M48×3-4 h。
2、產品加工工藝分析
通過對產品結構和技術要求的分析,找出該螺栓加工的難點:
(1) 該螺栓的兩端螺紋及中間桿身的同軸度要求高,而且該螺栓的長度較長,為645 mm,桿身直徑為41 mm,長徑比接近16∶1,剛性較差,加工較為困難。
(2) 該螺栓兩端均為M48×3-4 h的螺紋,螺紋等級要求高,采用傳統的加工方法,很難保證螺紋精度。
(3) 該螺栓批量大,每臺機體需48根氣缸蓋螺栓,采用傳統的加工方法加工效率低、生產周期長,無法滿足生產需求。
3、優化加工方法解析
3.1 以車代磨
傳統的加工方法,為保證工件的精度,一般采用磨削的方式加工螺栓的桿身及兩端螺紋檔。由于以前螺栓批量小,該加工方式的缺點沒有完全呈現出來,但隨著螺栓的大批量生產,該加工方式已無法滿足生產需求,必須采用新的加工方法,提高生產效率。
通過對螺栓技術要求分析,結合公司現有設備,計劃采用車削方式代替磨削方式加工螺栓的桿身。通過前期試驗發現車削加工存在2個問題:螺栓同軸度和表面粗糙度出現超差,無法滿足設計要求。
針對上面問題,分析其產生原因并進行攻關。
(1) 螺栓同軸度超差。
原因分析:螺栓剛性差,加工時容易產生振動;公司現有數控車床,長時間車削長度小于500 mm的產品,導致機床導軌前后段磨損情況不同。
解決方案:首先合理選擇加工刀具,半精車時采用負型刀,提高加工效率,降低生產成本。精車時采用正型刀,減小刀具切削阻力,同時優化切削參數,通過不斷試驗,合理選擇吃刀量、進給速度,避免刀具與工件產生共振,有效控制工件加工過程中的振動。其次請求設備維修部門對機床導軌進行鏟刮,保證機床導軌整體的平整度,提高機床的加工精度。
(2) 螺栓表面粗糙度差。
原因分析:螺栓材料熱處理后韌性好,車削加工時不容易斷屑,鐵屑纏繞在螺栓桿身上,拉傷螺栓表面;車削過程中工件振動,工件表面存在振紋,影響表面粗糙度。
解決方案:為了提高零件加工的斷屑性,首先與刀具供應商協商合理選擇加工刀具的斷屑槽形狀,同時優化切削參數,合理選擇吃刀量增加切削進給,提高斷屑能力。其次,自制斷屑塊(見圖2),將斷屑塊固定在刀具下端,改變鐵屑的流向與長度,保證加工過程中的良好斷屑。同時為有效消除車削振紋,須先調整車床主軸中心線與尾座中心線同軸,并與車床大導軌平行,允差應小于0.02 mm;刀具選擇上注意選擇75°~90°主偏角的車削刀具,使其加工工件時產生的徑向切削力最小,而讓刀片刃口產生的軸向力最大,并減小切削深度,增大進給量。
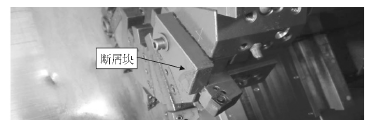
圖2 自制斷屑塊
通過攻關解決了車削存在的問題,保證了產品質量。為驗證車削加工桿身與磨削加工桿身加工效率的不同,選取相同數量的螺栓,分別采用2種方式進行加工,并對產品的加工時間進行統計,其平均加工時間如表1所示。
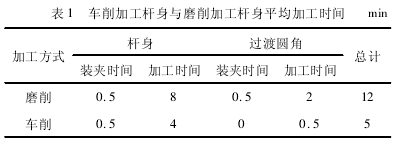
通過平均加工時間對比發現,車削桿身較磨削桿身的加工時間節約了約60%,加工效率提高。
3.2 滾壓加工螺紋
螺栓兩端的螺紋要求高,原加工方法是采用普通車床車削螺紋,車削效率低,同時由于螺紋長度較長,車削時容易產生振刀,螺紋表面粗糙度差,加之螺栓材料強度高、韌性好,刀具磨損快,螺紋尺寸不穩定。同時該螺栓組裝時需要進行拉伸試驗,由于車削螺紋強度低,拉伸時螺紋容易變形,導致螺母無法裝配。
通過對螺紋加工性能的分析,結合公司現有螺紋加工設備和先進的螺紋加工方法,計劃采用滾壓的方式加工螺紋。為了驗證滾壓方案的可行性,首先對螺紋滾壓力進行計算。
螺紋滾壓力F簡易計算公式:

通過查閱相關資料得出相關參數的數值:材料布氏硬度:HB296~350選上限值HB350、螺栓材料系數Z=4、材料延伸率A=10%、螺紋螺距P=3、螺栓有效長度為L:116~140 mm,選長端140 mm。
參考壓力計算:

考慮1.2~1.5倍的保有量,滾壓所需提供滾壓力F1=1.2×F=57.36 Tnos、F2=1.5×F=71.7Tnos,而公司現有63 Tnos的滾絲機,滿足滾壓要求,滾壓方案可行。
螺紋滾壓是一種不去除材料的成型工藝,即用成型的滾壓模具使工件產生塑性變形以獲得螺紋的加工方法,見圖3。

圖3 螺紋滾壓加工
通過對2種螺紋加工方式進行對比,滾壓制作螺紋的優點突出。
(1) 滾壓制作螺紋精度高。
滾壓制作螺紋時,螺紋的精度主要取決于滾壓坯的尺寸精度與滾壓模具的精度。由于每批次螺栓的原材料及熱處理存在差異,導致螺栓滾壓時延伸量不同,影響螺栓的精度,因此每批次螺栓滾壓坯的尺寸,是通過試滾確定的,即每次螺栓批量加工滾壓坯前,先試加工幾根,然后滾壓,確定滾壓精度后,再批量加工,有效保證螺紋滾壓坯的尺寸精度。同時,對采購的滾壓模具,進行合格性驗證,嚴格控制滾壓模具的精度,加之滾壓模具的使用壽命遠大于車削刀具的使用壽命,因此滾壓制作螺栓的加工精度高、穩定性好。
(2) 滾壓制作螺紋加工效率高。
螺栓的滾壓是一種一次成型工藝,無須多次進刀,因此加工時間較車削短。同時滾壓加工螺紋時,螺栓的固定裝夾較車削簡單方便,節約了大量的固定、裝夾時間。為驗證車削螺紋與滾壓螺紋加工效率的差異,選擇相同數量的螺栓,分別采用2種方式進行加工,平均加工時間統計如表2所示。
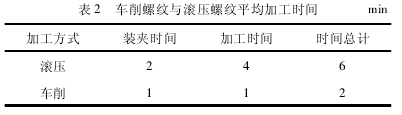
通過加工時間對比發現,滾壓制作螺栓的加工效率較車削提高了2倍。
(3) 滾壓制作螺紋強度高、表面粗糙度好。
滾壓制作螺紋是一種無屑螺紋成型工藝,是通過滾壓模具擠壓坯料,使其發生塑性變形,按滾壓模具的形狀形成螺紋。
滾壓制作螺紋與車削螺紋微粒流之間的區別如圖3所示。可以明顯地看出,滾壓螺紋部分,材料出現塑性變形,使表層組織冷硬化和晶粒變細,形成殘余的應力層,產生額外的拉伸強度,提高了螺紋的強度和硬度。同時滾壓技術也是一種壓力光整加工,利用金屬在常溫狀態的冷塑性特點,利用滾壓模具對工件表面施加一定的壓力,使工件表層金屬產生塑性流動,減小工件表面的凹凸峰谷之間的落差,從而達到較高的表面粗糙度。
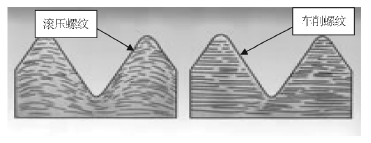
圖4 滾壓制作螺紋與車削螺紋微粒流之間的區別
(4) 滾壓制作螺紋生產成本低。
滾壓制作螺紋,采用不去除材料的方式加工螺紋,螺紋滾壓前尺寸一般為螺紋的中徑尺寸,而螺紋車削前的尺寸,一般為螺紋的大徑尺寸,因此滾壓制作螺紋比車削螺紋所需的坯料的尺寸小,對于大批量生產來說,這是一個很可觀的數字,降低了生產的成本。
4、結束語
本文通過車削、磨削及滾壓3種加工方式的優缺點對比,結合高強度精密螺栓的結構特性和技術要求,采用了以車代磨、以滾代車的加工方法,對高強度精密螺栓的加工方法進行了優化、改進,提高了螺栓的產品質量和加工效率。然而,隨著加工刀具、設備及加工技術的不斷進步,產品的加工方法也必須及時地優化、改進。
投稿箱:
如果您有機床行業、企業相關新聞稿件發表,或進行資訊合作,歡迎聯系本網編輯部, 郵箱:skjcsc@vip.sina.com
如果您有機床行業、企業相關新聞稿件發表,或進行資訊合作,歡迎聯系本網編輯部, 郵箱:skjcsc@vip.sina.com
更多相關信息