冷鐓機床身再設計孔洞的形狀優化
2017-7-21 來源:湖北理工學院 作者:何 彬
摘要:針對冷鐓機床身的拓撲優化在剔除材料的同時削弱了床身的整體力學性能,提出在冷鐓機床身結構拓撲優化后的再設計孔洞區域進行形狀優化,即以床身多約束拓撲優化后的再設計孔洞,作為形狀優化的設計變量,建立多邊界的形狀優化模型;描述了形狀優化中的 Laplacian 光順算法,構建了冷鐓機床身再設計孔洞的形狀優化過程,并在 Abaqus中分別實現了某型號冷鐓機床身再設計后單一孔洞和多孔洞的形狀優化,分析了不同優化結果對床身整體性能的影響,驗證了所提出方法的有效性。
關鍵詞:冷鐓機;床身;孔洞;拓撲優化;形狀優化
1.引言
鍛壓機床是機床中鋼材消耗量最大的一類機床,而床身又是鍛壓機床中占體積和重量比重最大的一部分,對床身進行合理減重是實現鍛壓機床輕量化的關鍵[1]。冷鐓機是典型的鍛壓機床,拓撲優化是冷鐓機床身輕量化設計中最常見也是最有效的方法之一,但是由于拓撲優化過程中材料的刪減不同程度削弱了冷鐓機床身整體力學性能,而材料刪減所形成孔洞的形狀是影響應力、變形等指標的關鍵因素[2-3],因此,將拓撲優化和形狀優化有機結合是提高床身輕量化設計質量的重要途徑。提出針對冷鐓機床身結構拓撲優化后的再設計孔洞進行形狀優化,是在保證減輕床身重量的前提下,盡可能通過對拓撲優化后再設計區域的形狀優化來改善床身的整體力學性能,從而提高床身輕量化設計的質量。
2.形狀優化模型
形狀優化通過使得某些物理量達到特定的邊界要求,來實現設計區域幾何形狀的改變,以優化結構、改善相關性能[4]。形狀優化所尋求的目標可以是最小化結構面積或體積、應力集中系數,也可以最大化結構的疲勞壽命等。同時,區域邊界還必須要保持光滑的連續性條件,優化的形狀邊界須滿足可制造性原則。在基于有限元分析技術的形狀優化中,最大缺點是在優化迭代過程中,容易發生有限單元網格的畸變或扭曲,因此必須要滿足網格的最大曲扭要求。設計變量一般以設計區域邊界形狀的幾何參數為主,如單元網格的節點坐標等,也可選擇非幾何參數如虛荷載變量等[5-6]。形狀優化是邊界形狀的不斷迭代過程。優化區域形狀的改變會導致應力的重新分布,一旦應力分布有利于優化函數的收斂,同時約束條件也得到滿足,則會以實時的邊界形狀為優化變量,進行下一次迭代;若不滿足約束條件或不利于優化函數的收斂,則以新的邊界形狀進行迭代,直到條件滿足為止[6-8]。冷鐓機床身形狀優化是對拓撲優化后所設計的孔洞進行優化,由于孔洞的數量大于 1 且離散分布,因此可界定為多邊界的形狀優化問題,設待優化孔洞形成的邊界數量為 n,多邊界的形狀優化問題可以描述為[8-10]:
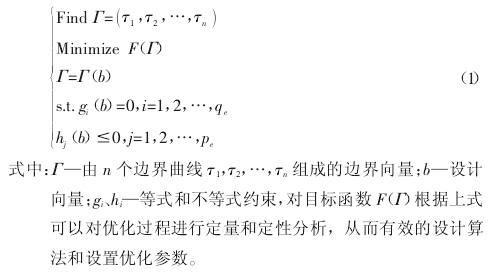
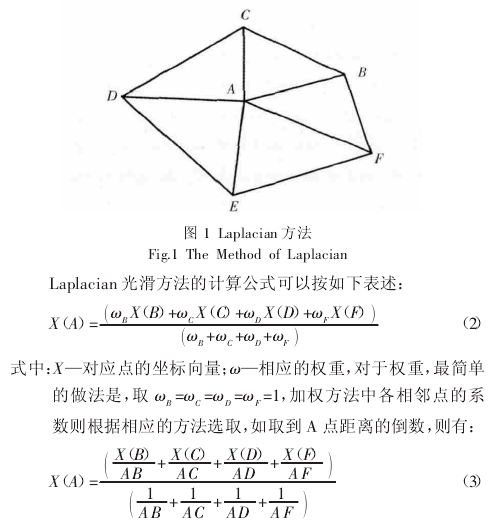
上述 Laplacian 以及各種加權方法的實現都相對簡單,計算速度極快,效率高,在一般區域都只要計算數次就能獲得理想的結果,但當區域內網格品質較差、網格狹長或存在小孔洞時,多會產生無效網格,因此,在很多形狀優化的軟件中,往往采用帶約束的 Laplacian 光滑方法,主要針對網格品質引入判斷量,根據網格點移動前后的品質逐一比較,僅在網格品質提高時才進行網格點的移動,否則,當品質較差時則取消移動,保持先前的網格點不動。如不能提高品質時,則將移動距離減小為原來的一半,到指定次數仍不能提高網格品質,則保持點不動;從而保證所有網格品質的提高,減少計算量,改善優化性能。
4.優化過程模型
冷鐓機床身拓撲優化在于通過剔除材料而達到減重的目的,形狀優化是在不改變減重效果的前提下,對拓撲優化后所設計的孔洞形狀進行優化,使形狀更趨于合理,從而改善床身的整體力學性能。通過拓撲和形狀優化的聯合作用,形成具有合理結構的孔洞。其求解的順序可以描述為:
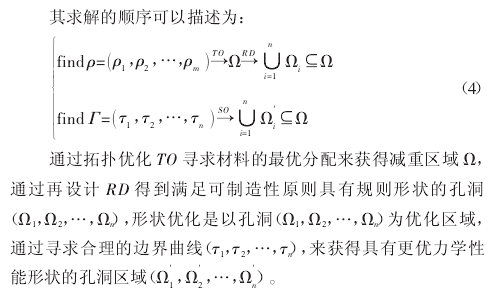
冷鐓機床身形狀優化的實現流程,如圖 2 所示。在優化過程中,首先針對所有的再設計孔洞區域進行形狀優化,也就是多邊界的整體形狀優化,然后再分別以單獨的孔洞區域為對象進行形狀優化,對兩種優化方案進行分析,由于同一孔洞在整體和單獨優化后形狀改變的程度,決定了該區域對床身整體機械性能的影響程度,從而可以確定出關鍵區域,并綜合床身的可制造性原則,選定最優的設計方案。
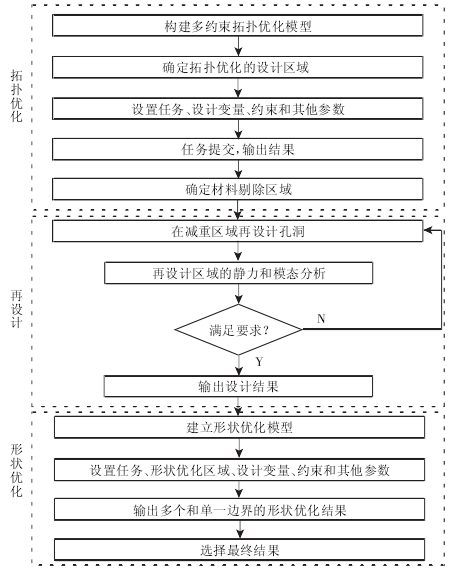
圖 2 冷鐓機床身結構形狀優化的實現流程
5.應用實例
以某型號冷鐓機床身為實例,驗證所提出方法的正確性。在工作過程中,冷鐓機床身主要承受鐓斷力的作用。該冷鐓機床身的受力分析和初始設計參照文獻[2],拓撲優化模型采用應變能最小為目標函數,以體積、最大應力、最大位移等為約束,經過 10 次設計循環,得到剔除孔洞后的拓撲優化結果。根據拓撲優化結果,在材料剔除區域按照可制造性原則,設計孔洞形狀[2],如圖 3 所示。
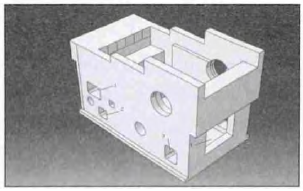
圖 3 再設計結果
5.1 再設計孔洞的形狀優化
形狀優化是為了進一步改善床身的力學性能,在本例中,主要對再設計的孔(1~4)進行形狀優化,為了分析不同再設計孔洞對床身力學性能的影響,首先設置 4 個孔洞為形狀優化區域,以再設計床身的最大主應力最小化為優化目標,體積不變為約束,采用帶約束 Laplacian 光順算法,驗證 4 個孔洞整體形狀優化結果和收斂過程,如圖 4 所示,在經過 14 次設計循環之后,整體形狀優化基本上趨于收斂。從優化后的應力云圖和位移云圖可知,整體形狀優化后,在不改變體積的前提下,床身最大應力和位移分別從由優化前的 115MPa 和 0.679mm 分別減少到 58.59MPa 和0.06098mm,床身力學性能明顯得到了改善。
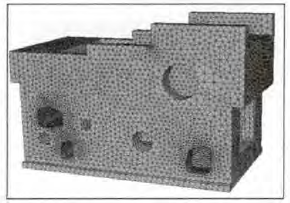
圖 4 多孔洞整體形狀優化結果
其次分別以孔(1~4)為形狀優化區域,優化函數、體積約束和其它參數都不變,可以得到單一孔洞的形狀優化結果,如圖 5所示,圖中 a)-d)分別表示了孔(1~4)的形狀優化,與整體形狀優化相比較,單一孔洞形狀優化的最大應力和位移基本上沒有多大改變,但是從優化后的形狀看(主要從優化后孔的大小和曲線形狀進行評價),孔 1 和孔 2 的形狀改變較大,而孔 3 和孔 4 形狀改變較小。
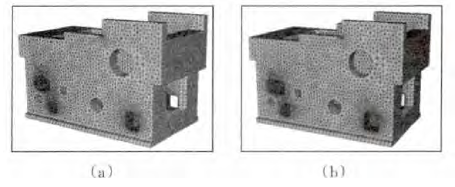
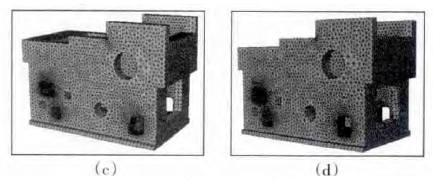
圖 5 單一孔的形狀優化
5.2 結果分析
從本例中冷鐓機床身的形狀優化結果可知,4 個孔洞整體形狀優化與單一孔洞形狀優化后的最大應力和位移基本不變,孔 1和孔 2 的形狀改變較大,而孔 3 和孔 4 形狀改變較小,說明孔 3和孔 4 的形狀對床身最大應力和位移影響較大,因此如果要進一步改善拓撲優化后再設計床身的力學性能,可以著重考慮孔 3 或孔 4 的形狀優化結果,而無需改變再設計床身中孔 1 和孔 2 的形狀,從而簡化冷鐓機床身的設計過程,提高設計效率。形狀優化可明顯改善拓撲優化后冷鐓機床身的力學性能,從而使設計更趨于合理。
6.結論
提出冷鐓機床身拓撲優化后再設計孔洞的優化,是拓撲和形狀優化的協同求解過程,拓撲優化用于減重,形狀優化是對拓撲優化后設計區域的邊界求解,結果表明,整體和單一孔洞的形狀優化對床身力學性能的影響差異不大,不同位置的孔洞形狀對床身最大應力和位移有不同程度影響;通過優化,不僅冷鐓機床身重量減輕了,而且相比拓撲優化后的再設計床身,最大應力和位移分別也有一定程度的下降,說明將拓撲與形狀優化結合起來具有必要性和有效性。
投稿箱:
如果您有機床行業、企業相關新聞稿件發表,或進行資訊合作,歡迎聯系本網編輯部, 郵箱:skjcsc@vip.sina.com
如果您有機床行業、企業相關新聞稿件發表,或進行資訊合作,歡迎聯系本網編輯部, 郵箱:skjcsc@vip.sina.com